Ein automatisierter Ansatz zur Überbrückung von Tool-Lücken und zur Verbesserung von Leistungsmetriken
Optimierung des Batteriedesigns
Erfahren Sie, wie eine einheitliche Methodik für die Entwicklung von Batteriepacks die Lücken zwischen bestehenden Werkzeugen schließt und eine effiziente Optimierung von Parametern wie Energiedichte, Lebensdauer, Sicherheit und Kosten ermöglicht.
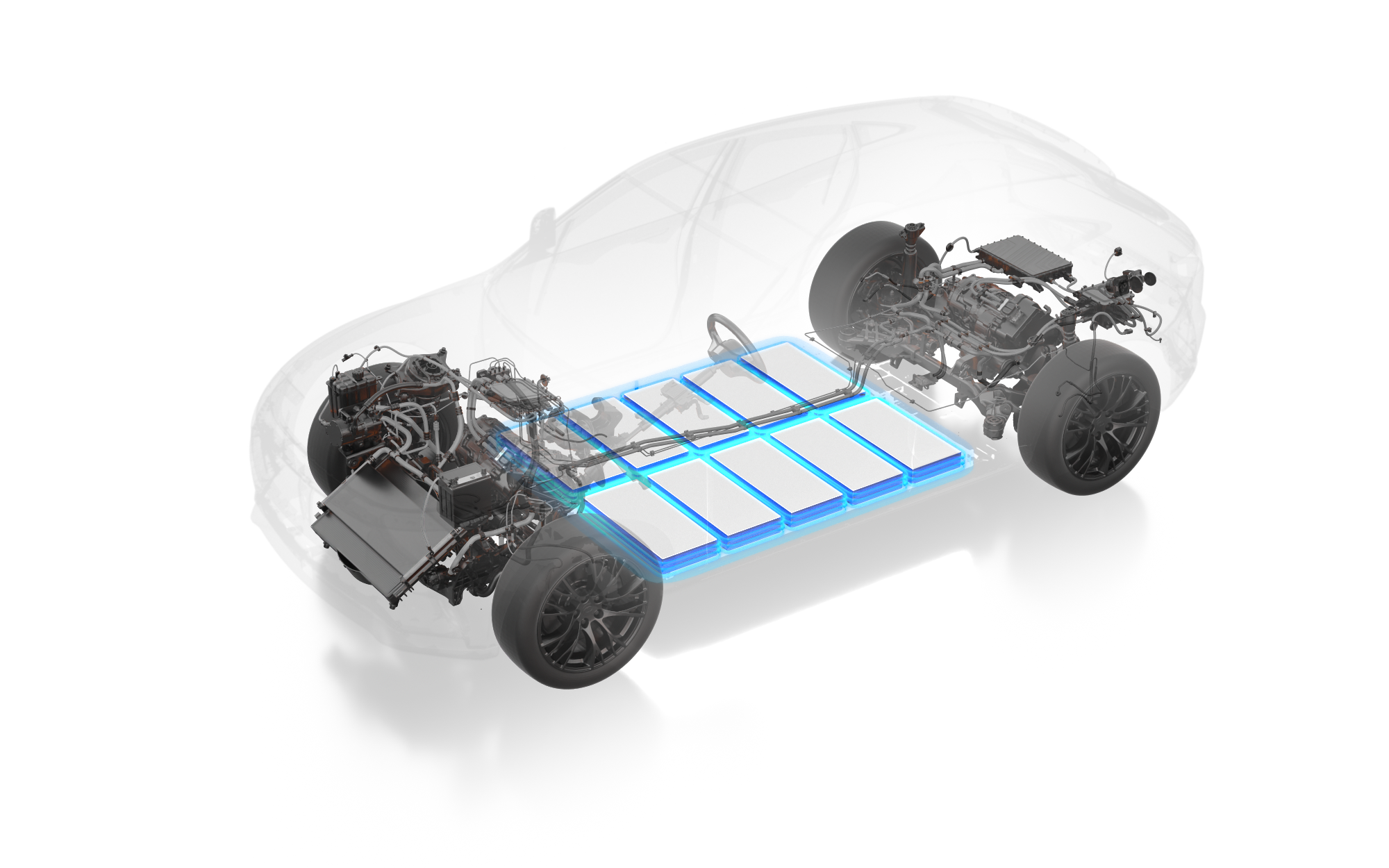
Challenge
Die moderne Batteriesystemtechnik bewegt sich im Spannungsfeld mehrerer anspruchsvoller Zielvorgaben, wobei jeder Parameter seinen eigenen Einfluss auf die Gesamtleistung und Effizienz des Designs hat. Die Ingenieure stehen vor der großen Herausforderung, die Energiedichte, gemessen in kWh/kg, zu optimieren, die Lebensdauer, gemessen in Jahren oder Betriebszyklen, zu gewährleisten, die höchsten Sicherheitsstandards zu erfüllen und all dies innerhalb bestimmter Kostenparameter zu erreichen.
Batteriesystemingenieure stehen vor der komplexen Aufgabe, verschiedene Ziele miteinander in Einklang zu bringen: Energiedichte (kwh/kg), Lebensdauer (Jahre oder Zyklen), Sicherheit und Kostenfaktoren. Die derzeitigen Werkzeugketten können diese Parameter nicht gleichzeitig auf mehreren Ebenen berücksichtigen, was zu fragmentierten und sequentiellen Arbeitsabläufen führt. Aktualisierungen von CAD-Tools sind aufgrund der Komplexität der Bauteile oft zeitaufwändig und behindern schnelle iterative Prozesse. Darüber hinaus erfordern Konstruktionsänderungen häufig manuelle Eingriffe durch CAE-Fachleute, da es keine robuste Assoziativität gibt, was die Rückkopplungszeit verlängert.
Solution
Synera ist als umfassende Softwareplattform konzipiert, die ein effizientes Toolset für die Entwicklung von Batteriepacks bietet, wobei der Schwerpunkt auf der Integration von Design, CAx und zeitnaher KPI-Auswertung liegt. Im Wesentlichen vereinfacht Synera nicht nur den komplexen Batterieentwicklungsprozess, sondern beschleunigt ihn auch, fördert Innovationen und sichert Wettbewerbsvorteile auf dem Markt.
Entdecken Sie die Feinheiten unserer integrierten Arbeitsabläufe, die sorgfältig entwickelt wurden, um den Entwicklungsprozess des Batteriepack-Designs zu rationalisieren:
- Zell-/Block-Entwurfsphase: Der grundlegende Input sind die Daten der einzelnen Batteriezellen. Anstatt sich jedoch mit den Details des Entwurfs zu befassen, steuert der Ingenieur den Arbeitsablauf von einem strategischen Standpunkt aus, indem er Beschränkungen und Ziele, insbesondere in Bezug auf Kapazität und Spannung, festlegt. Innerhalb dieses Rahmens wird eine methodische Versuchsplanung (Design of Experiments) durchgeführt, um die am besten geeignete Blockgröße und -konfiguration zu ermitteln. Das Ergebnis ist die optimale Blockgeometrie.
- Packoptimierung: In dieser Phase werden die Spezifikationen festgelegt, die später für den Entwurf der Batteriemodule und -packs verwendet werden. Es wird versucht, die optimale Anzahl von Modulen und ihre räumliche Anordnung innerhalb des größeren Rahmens des Batteriepacks zu definieren. Diese Phase wird durch die Erkenntnisse aus der vorhergehenden Blockgeometrie bereichert. Folglich wird ein nachfolgendes Design-Experiment durchgeführt, um die optimale Anzahl von Blöcken pro Modul zu bestimmen. Anschließend wird ein fortschrittlicher Verschachtelungsalgorithmus verwendet, um die optimale Packungsstrategie zu bestimmen. Das Ergebnis dieser Phase ist ein detailliertes Verständnis der Modulabmessungen, ihrer spezifischen Ausrichtung und ihrer genauen Positionierung im gesamten Designraum des Batteriepacks.
- Moduldesign und Optimierung der Eigenschaften: Der Arbeitsablauf umfasst eine detaillierte Untersuchung des Moduldesigns. Der Schwerpunkt liegt auf der Integration einer Kühlplatte, die durch eine rigorose thermische Analyse unterstützt wird. Auf der Grundlage der in den vorhergehenden Phasen gewonnenen Daten ermöglicht der Arbeitsablauf schließlich die Montage (Zellen, Blöcke, Kühlplatte) des fertigen Batteriemoduls, das in das endgültige Pack-Design integriert werden kann.
- Package Design und Strukturoptimierung: Das Hauptziel ist die Fertigstellung des Package Designs. Dies beinhaltet die Integration von Aspekten wie Strukturanalyse, Leichtbauoptimierung und die Anordnung der endgültigen Verkabelung. Um dies zu erreichen, werden vorhandene Daten wie die Konstruktionsparameter des Batteriepacks und der vormontierten Module berücksichtigt. Auf Basis dieser Daten wird eine Reihe von Finite-Elemente-Analysen (FE) durchgeführt. Diese Analysen beinhalten Modalanalysen und untersuchen die Eignung verschiedener Materialien wie Aluminium und Verbundwerkstoffe, um einen tieferen Einblick in die optimale Materialauswahl zu erhalten. Leichtbaumethoden, insbesondere die Topologieoptimierung, werden nahtlos mit externen Tools wie Altair OptiStruct integriert. Im weiteren Designprozess sind iterative CAD-Verfeinerungen unerlässlich. Diese Verfeinerungen umfassen automatische Rekonstruktionen basierend auf den Ergebnissen der Topologieoptimierung und einen robusten parametrischen Design-Workflow, der die Genauigkeit und Integrität des Designs sicherstellt. Syneras interner Path Finder Algorithmus ergänzt diesen Prozess und rationalisiert die komplexe Aufgabe der Modulverkabelung. Am Ende dieser Phase wird ein umfassender Überblick über die Key Performance Indicators (KPIs) gegeben, wobei Metriken wie Spannung, Strom und Komponentengewicht hervorgehoben und die Auswirkungen jeder Designentscheidung auf diese primären Metriken erläutert werden.
More about this workflow
Benefits
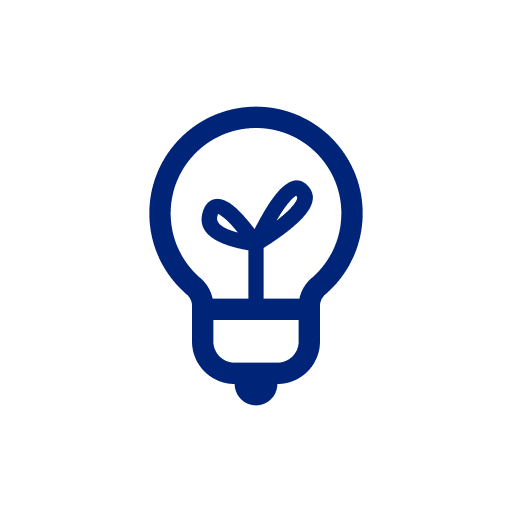
Integrierter Entwurf und Analyse
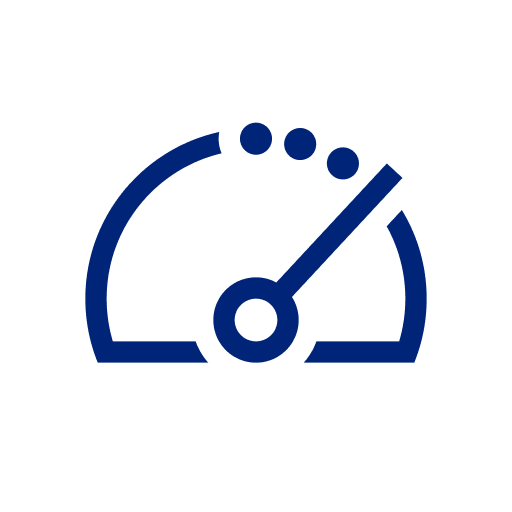
Schnelle KPI-Bewertung