Maßgeschneiderte Sportgeräte aus dem 3D-Drucker
Anschütz ist der unangefochtene Marktführer bei Biathlongewehren. Für 97% aller Biathleten weltweit ist Anschütz das Sportgewehr der Wahl.
Umlaut und Anschütz entwickeln mit generativer Technik ein völlig neuartiges Biathlongewehr. Benjamin Wirthen gibt Einblicke in einen faszinierenden Prozess.
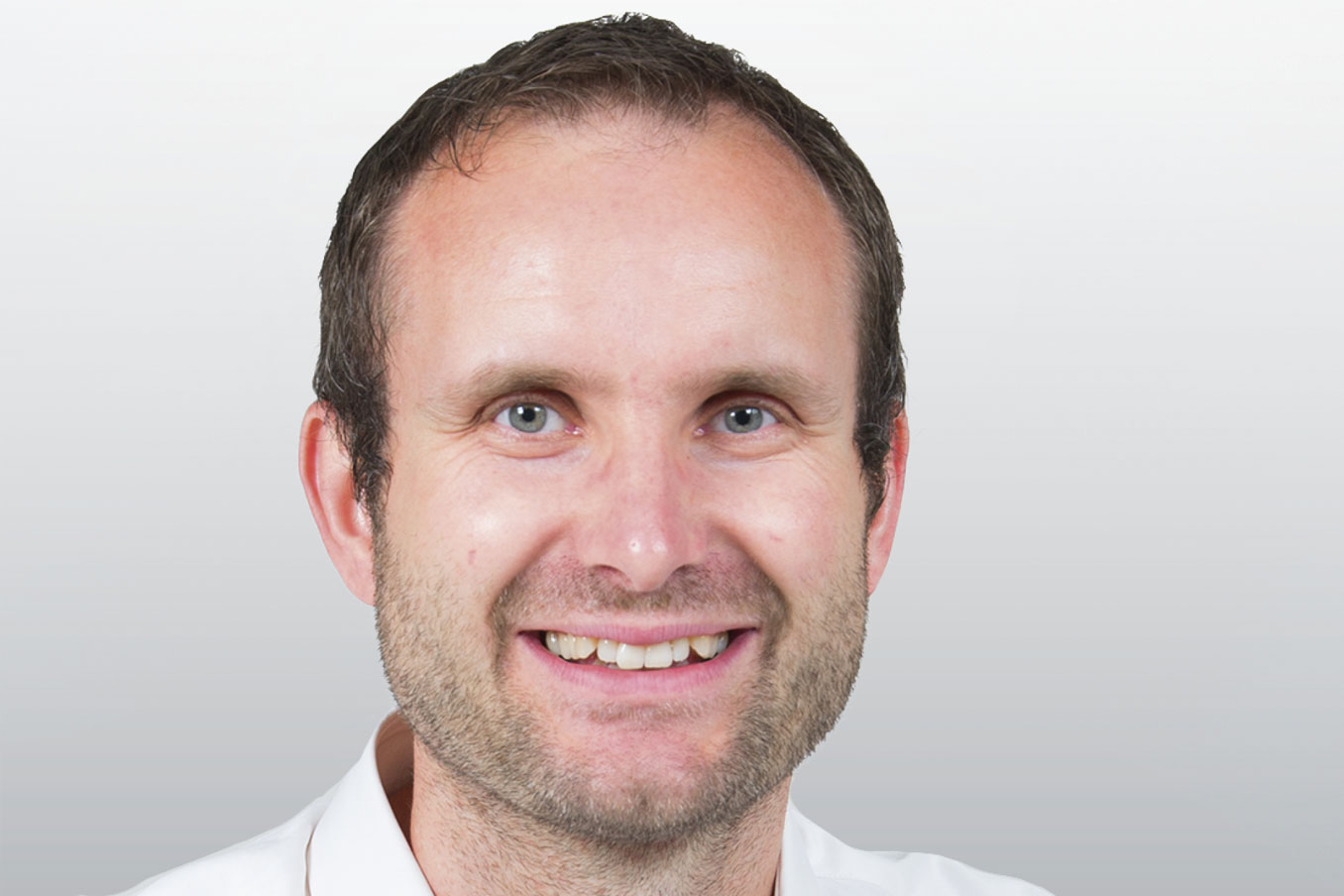
Biathlon ist eine der beliebtesten Wintersportarten. Das hängt sicher mit der spannenden Kombination von zwei Sportarten zusammen: Skilanglauf und Schießen - also Ausdauer, Kraft und höchste Präzision zugleich. Welche Rolle spielt Ihr Gewehr für die Athleten?
Die Qualität der Sportwaffe ist in der Tat extrem wichtig. Es hängt vor allem vom Schaft ab, wie präzise der Sportler damit treffen kann. Der Schaft ist der hintere Teil des Gewehrs, den der Sportler in den Händen hält. Je besser dieser Griff ist, desto präziser sind die Schüsse. „Der Schütze schießt, der Schaft trifft“ ist ein deutsches Sprichwort.
Jetzt hat Anschütz zusammen mit Synera (früher ELISE) und dem Beratungs- und Ingenieurbüro umlaut einen völlig neuen Schacht entwickelt. Sieht er nur anders aus - oder steckt mehr dahinter?
Diese Innovation wird im 3D-Drucker hergestellt. Der Schaft wird also nicht aus einem Stück Holz gefräst, wie es früher der Fall war. Stattdessen ist er aus leichtem und dennoch sehr robustem Kunststoff gefertigt. Und das Wichtigste: Wir können jeden Schaft individuell an die Anatomie des Schützen anpassen. Bislang konnten sich nur wenige Spitzensportler eine solche Maßanfertigung leisten.
Was bedeutet Anpassung bei Sportgewehren?
Schaft und Griff passen sich den Proportionen der Arme, Hände und des gesamten Körpers des Sportlers an. Dadurch ist es möglich, auch nach mehreren Schüssen noch sehr genau zu treffen. Bisher hatten die meisten Athleten nur einige wenige Schaftvarianten zur Verfügung, aus denen sie das am besten geeignete Modell auswählten. Das war für sie natürlich nicht hundertprozentig treffsicher.
Dieses Gewehr sieht schon auf den ersten Blick anders aus. Der Schaft weist viele Aussparungen auf. Warum sind sie notwendig?
Tatsächlich haben wir nur genau die Menge an Material verwendet, die nötig ist, um die höchstmögliche Stabilität zu erreichen. Dieses Design wird durch den 3D-Druck ermöglicht. Dabei wird Schicht für Schicht Material aufgetragen, so dass das Endprodukt langsam wächst. Dieses Verfahren wird als additive Fertigung bezeichnet. Im Gegensatz dazu wird bei der Bearbeitung von Holz das Material mit einem Fräser, Meißel oder Bohrer abgetragen. Aussparungen und spezielle Oberflächenstrukturen wie bei unserem neuen Lager sind bei Holz nicht möglich.
Anschütz ist ein Unternehmen mit langer Tradition. Wie kam es zu der Entscheidung, in die Hightech-Produktion einzusteigen?
Wir sind immer auf der Suche nach Innovationen. Bei diesem wichtigen Projekt arbeiten wir mit Synera zusammen, einem innovativen Anbieter von Entwicklungssoftware. Deren Programm hat berechnet, wie das neue Gewehr gestaltet sein muss, um die Anforderungen bestmöglich zu erfüllen. Zunächst wurde aus den Grundanforderungen eine technische DNA des Schaftes erstellt. Die Software errechnet dann selbstständig das genaue Design jedes Schaftes. Wir geben im Vorfeld die anatomischen Daten des Sportlers ein und die Software übernimmt die Individualisierung. Das war früher unbezahlbar und hätte ewig gedauert.
Und wie erleben die Sportler das neue Gewehr?
Die Pistole vibriert beim Gebrauch weniger. Dies ist auf seine innovative Bettung mit einer oberflächlichen Wabenstruktur zurückzuführen. Die Bettung eines Schaftes ist das Geheimnis eines ruhigen Gewehrs: Sie stellt die physische Verbindung zum Sportler her. Diese wabenförmige Struktur ist in Holz nicht möglich. Nur die additive Fertigung in Kombination mit dem algorithmusbasierten Design von Synera hat uns diese Möglichkeit gegeben.
Ist das neue Gewehr dann nicht viel teurer als die Vorgängermodelle?
In der Tat wird die Individualisierung die Kosten letztlich nicht einmal um weniger als zehn Prozent erhöhen. Aber der Nutzen für die Athleten ist enorm. Wir haben unsere Innovation in der letzten Saison vorgestellt und sind auf großes Interesse gestoßen. Im nächsten Winter wird unsere Aktie zum ersten Mal im Wettbewerb zu sehen sein. Die Zwillinge Mareike und Sabrina Braun, genannt die Braunis, gehören zu den ersten Sportlern, die bereits mit dem neuen Gewehrschaft trainieren.