Automated design for WAAM
The coordination between design, FEA and manufacturing departments for the development of a wire-arc additively manufactured a-pillar takes too much time. That results in high development costs and limited design loops to find the optimal design. The manufacturing constraints were digitalized and integrated in a Synera workflow. The iteration between design, FEA and manufacturability ran automatically. This is how the team was able to find an optimal design and to save manual efforts and alignment meetings.
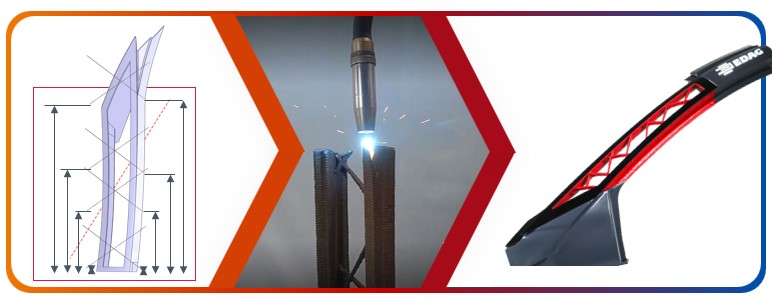
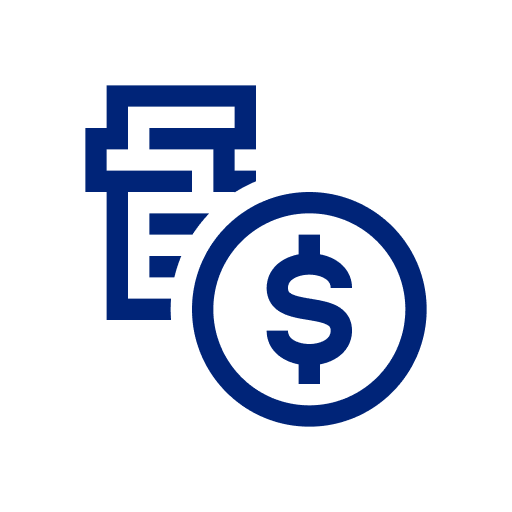
Positive ROI within first research project
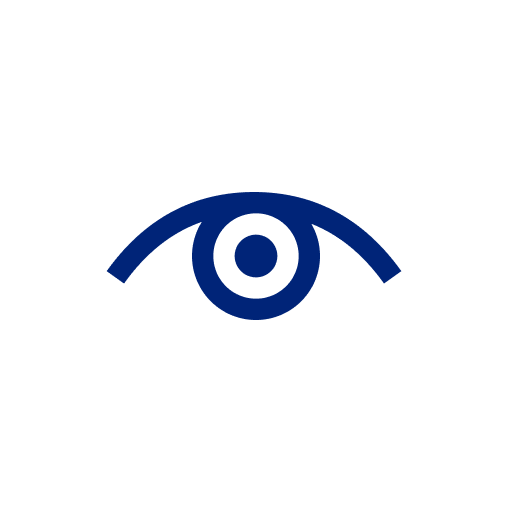
60 % Field-of-view gain
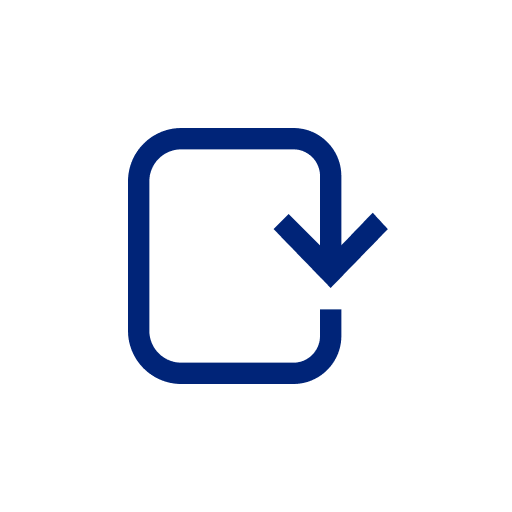
10x more possible iterations
I was caught in countless coordination meetings with different departments. It took more time to align then to design. That was too much for me! So, I digitalized the whole manual development process and created an automated workflow in Synera. Now Synera is performing all the iterations, and I can focus on creative tasks.
EDAG Group
EDAG is the world's largest independent engineering provider for automotive solutions, covering Vehicle Engineering, Electric Electronics, and Production Solutions. Their diverse teams of experts shape the future of mobility, offering comprehensive engineering services from concept to product development and turnkey production systems. As a technology leader, EDAG drive innovation in lightweight construction, electromobility, digitalization, and safety.