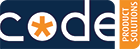
Assembly design and weld documentation for large machine enclosures
Code Product Solutions slashed FE model setup time by 60% and weld documentation time by 50% using an automated workflow, enabling faster design iterations and higher-quality modelling for complex machine enclosures.
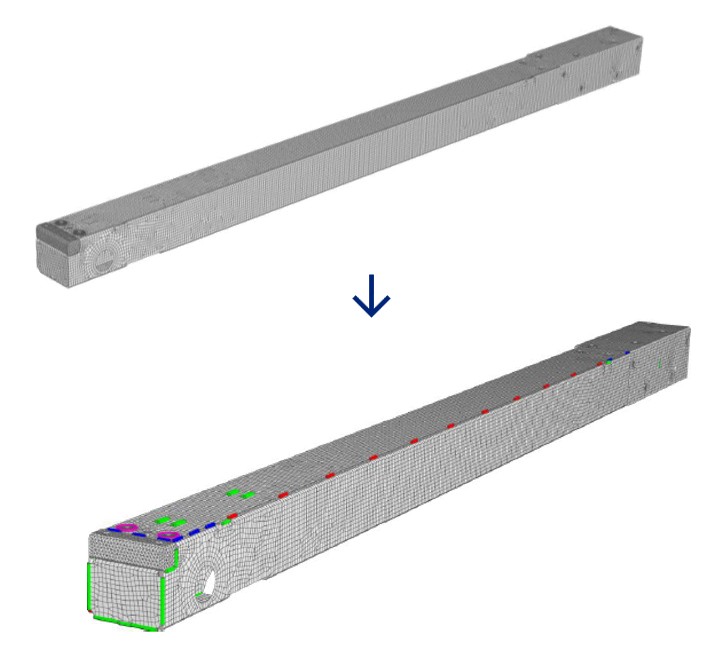
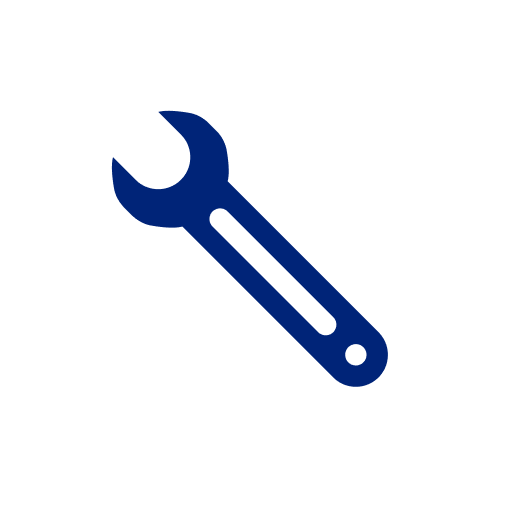
60% reduction in FE modelling time
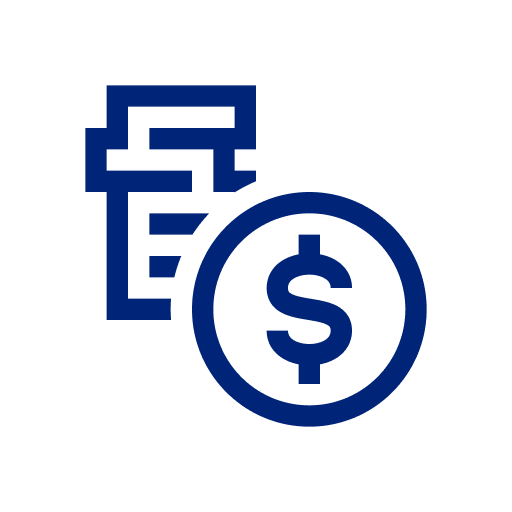
50% reduction in weld documentation setup
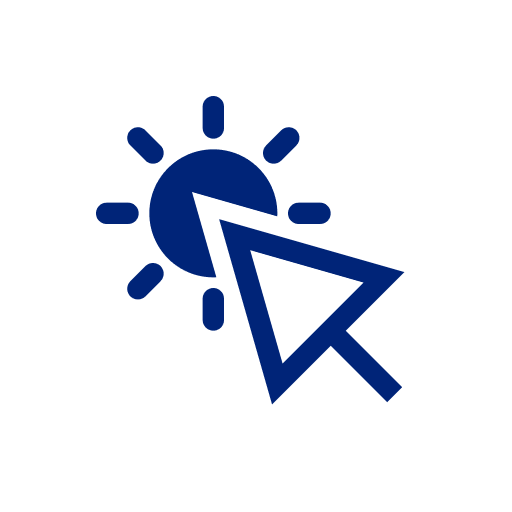
20% more efficient project management
Challenge
The design and modelling of large machine enclosures involved handling assemblies with more than 100 frame parts and 80 panels, typically made of folded and welded or riveted sheet metal. The traditional FE modelling process was manual, requiring engineers to individually identify parts, apply different meshing techniques (solid for machined parts and shell for sheet metal), and manually create bolt and washer imprints. This process is time-consuming and leading to significant delays when CAD models were updated late in the development cycle.
Moreover, weld documentation, which included creating and updating over 100 individual weld documents, was particularly challenging. The process required expert weld engineers, was labour-intensive, and could take over 2.5 weeks of work. Engineers had to manually update the weld documents every time a CAD model was modified, which slowed down the process. This lack of agility meant engineers couldn’t quickly adapt to design changes, leading to potential delays in project timelines. Every modification required manual adjustments, making it difficult to maintain momentum, especially with frequent updates. The need for a more efficient and responsive solution became evident as these delays also introduced potential quality issues and compromised overall project delivery.
By implementing an automated workflow, we reduced our FE modelling time by 60% and halved the time needed for weld documentation. This allowed us to handle complex assemblies with greater efficiency, delivering high-quality results while meeting tight deadlines even with last-minute design changes.
Code Product Solutions
Code Product Solutions is an engineering partner to product developers in all industries. We combine our expertise in materials, processes and design to help develop and improve a wide range of products.
Solution
The introduction of an automated workflow changed Code Product Solutions' FE modelling and documentation process. For the assembly's frame parts, the system automatically identified and filtered out machined and sheet metal parts. Machined parts were solid meshed, while sheet metal parts were shell meshed. The workflow automatically generated bolt and washer imprints and even modelled beams for bolts and bushes, ensuring consistency and speed. Furthermore, weld locations and layouts were predicted automatically, with the system exporting the weld geometry directly into CAD formats. The automated creation and handling of model variants allowed for quick adaptation to design changes without sacrificing accuracy or time.
- For the panels, the system applied similar efficiencies, automating the shell meshing of sheet metal parts and rivet modelling. The process automatically added assembly information, and both frame and panel models were exported as Optistruct models. This reduced the need for manual intervention and ensured consistency across different parts of the assembly. This automation reduces the modelling time from months to weeks.
- In terms of weld documentation, the new workflow brought significant improvements. The automation cut significantly the setup time, reducing what once took 100 hours down to 20 hours. The system automatically created the weld documents, applying predefined weld rules based on engineering standards. This automation made it possible to generate accurate, up-to-date 3D CAD models of welds and provided real-time updates as CAD models changed, further speeding up the entire process.
More about this workflow
Benefits
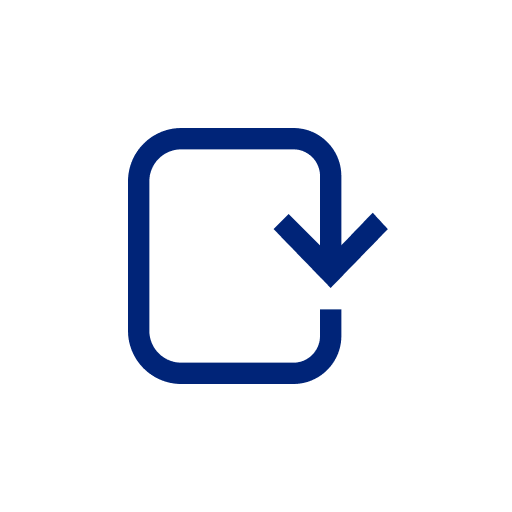
Automated FE for Assemblies
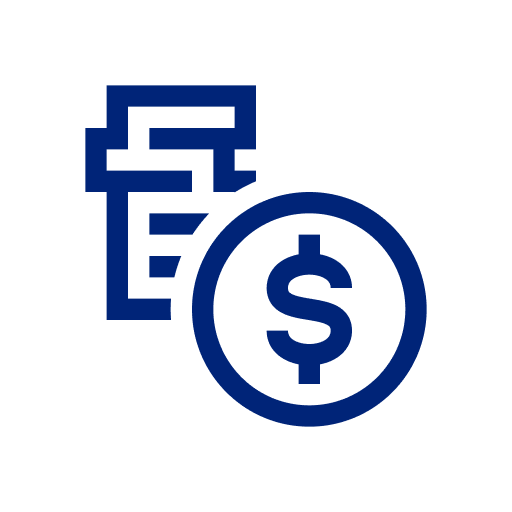
Save time and cost
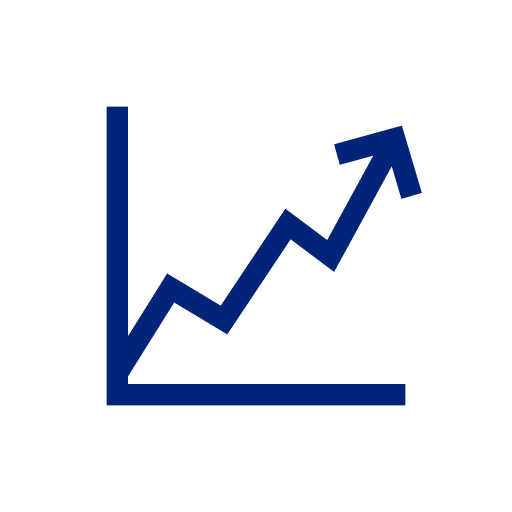
Reduction of manual tasks
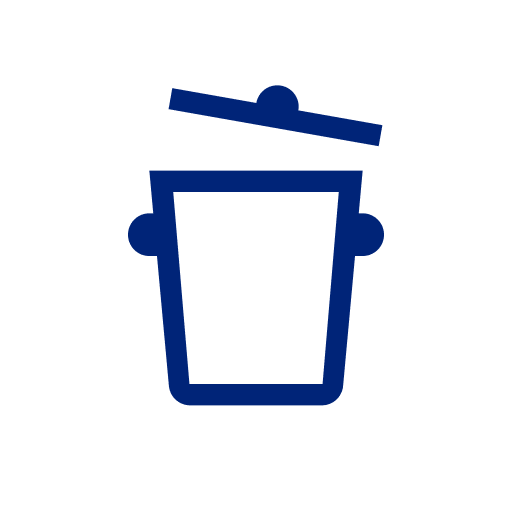
Avoidance of manual errors
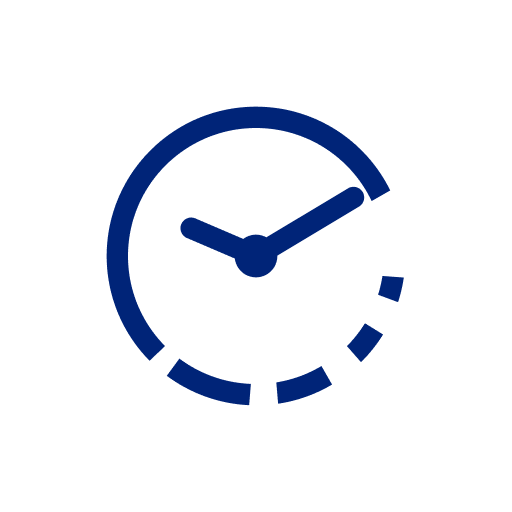
Reduction of Time-to-Market