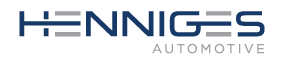
Antivibration center bearing for the power train
Automated development for die casting
The development process of die casting components is severely limited by manual process iterations. The digitalization and automation of the process leads to immense savings and an efficient strategy for part development of the future.
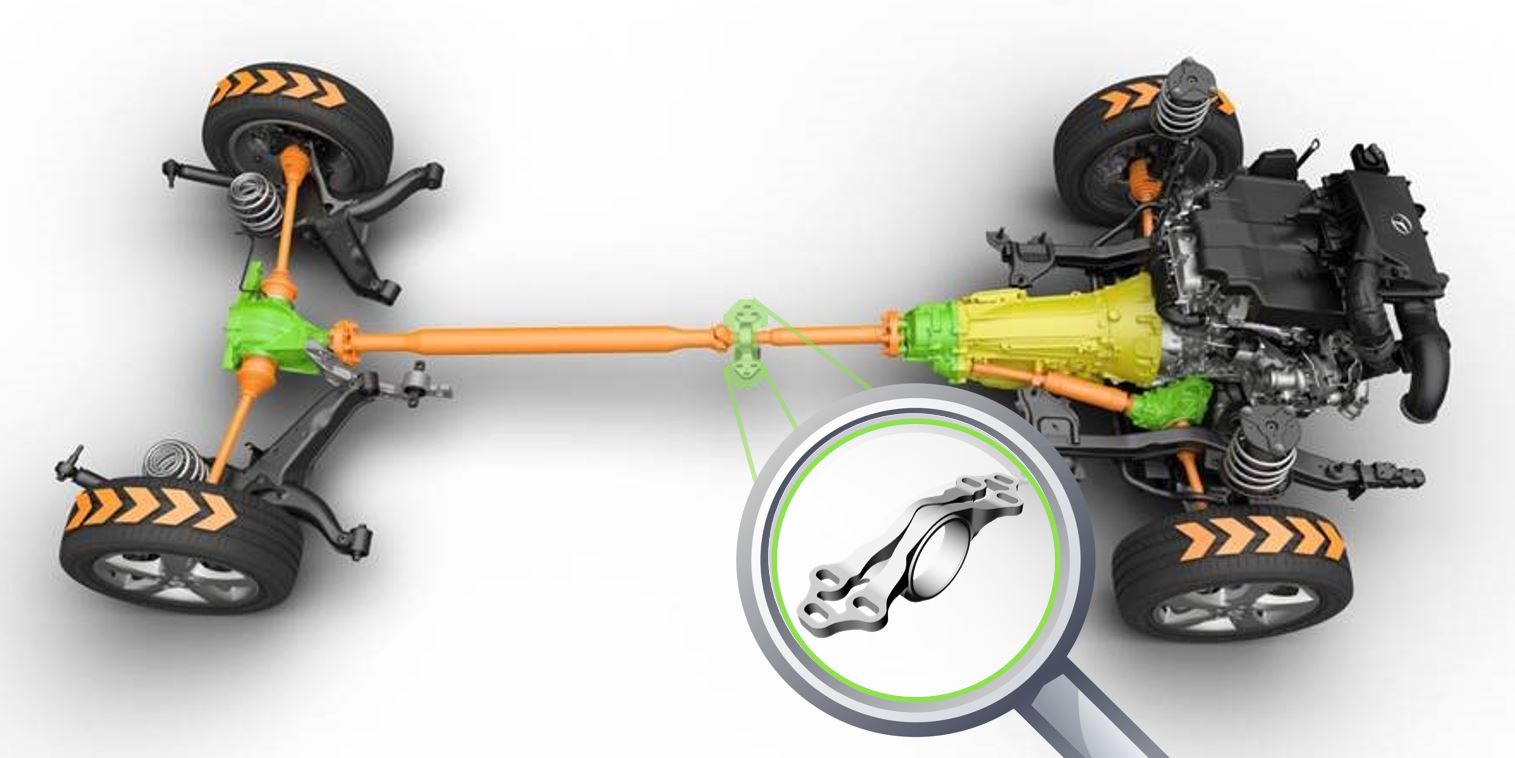
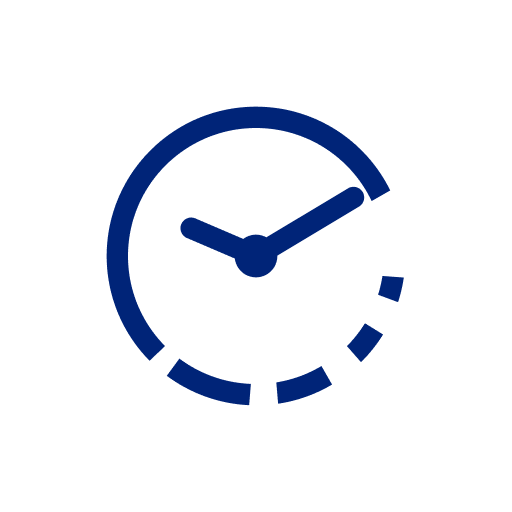
80% saved time
In comparison to a classical development
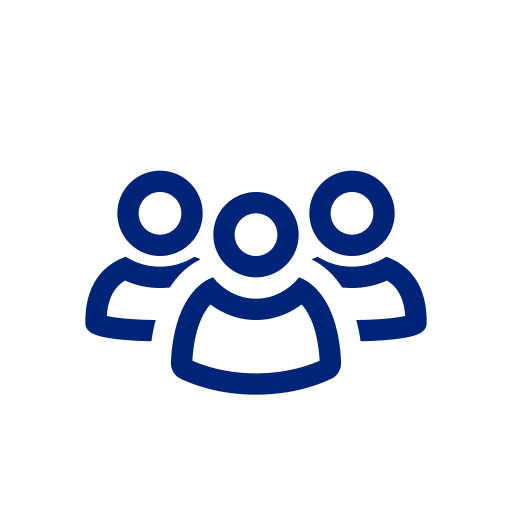
85% reusability
Copy & paste of the workflow for similar parts
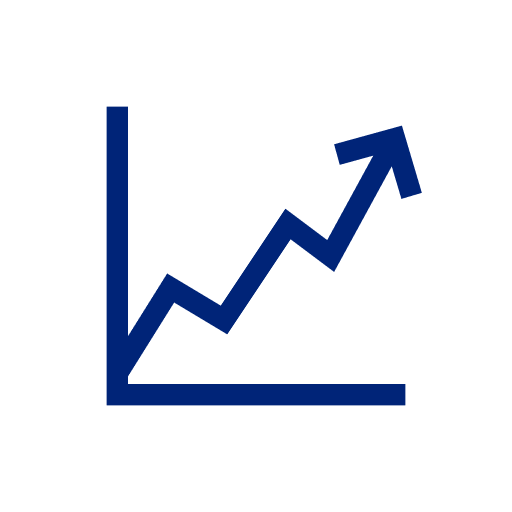
18% less weight
Improved performance and material reduction
Challenge
The engineering process of the center bearing for a van's powertrain includes design, simulation, and optimization steps and is not a straightforward process, but includes many manual iterations. To adapt the part to the performance requirements or to react to changes of the input data that occur quite often, the CAD design must be adapted again and again. And so, linked validation steps must also be repeated. All this means a high manual effort, especially for the designer.
Henniges Automotive
Henniges provides automotive original equipment manufacturers (OEMs) with sealing systems for doors, windows, trunks, lift gates, sunroofs and hoods. The company also supplies the automotive market with anti-vibration components and encapsulated glass systems. Headquartered in Auburn Hills, Michigan, Henniges sells to all major Automotive OEM customers and operates facilities in North America, South America, Europe and Asia with over 8,000 employees worldwide.
Solution
Henniges Automotive embraced the approach of Connected Engineering to accelerate the development processes for the center-bearing die-casting design. Synera's Connected Engineering allows digitalized engineering tasks to be used repeatedly. This was achieved by digitizing the development process in the visual programming platform.
The workflow is based on input data from Excel, includes a parametric CAD design, an automatic topology optimization reconstruction inside Synera and the connection to Altair Optistruct for topology optimization and FEA validation emphasizing real-time data exchange. The development process is run through automatically, so that validation iterations, last-minute changes to the input data, and the associated redesigns are carried out without any manual interaction - a revolutionary breakthrough in structural engineering.
More about this workflow
Benefits
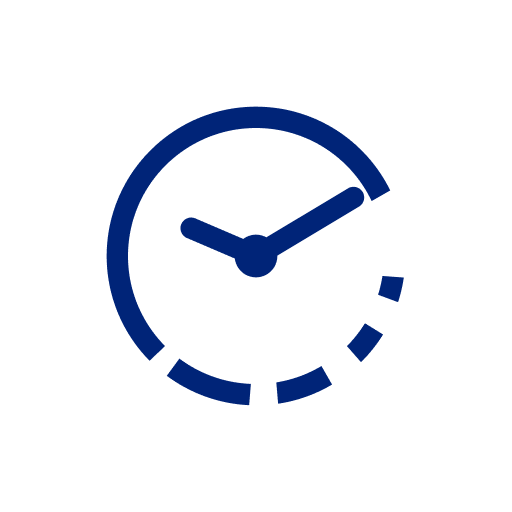
Reduction of Time-to-Market
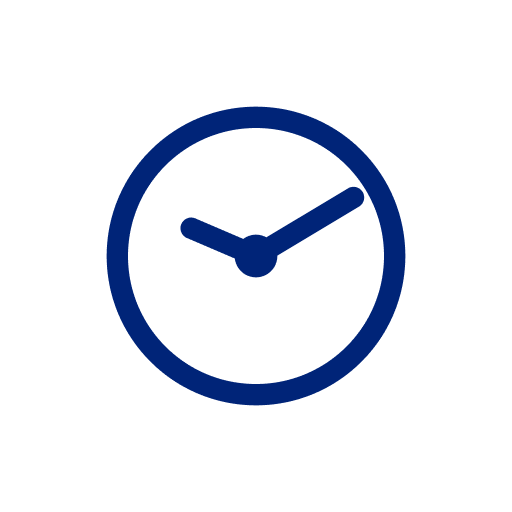
Save development time and cost through automation
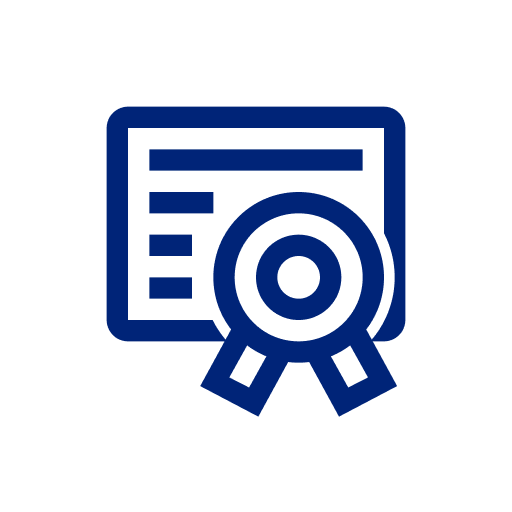
Knowledge storage through digitization of engineering
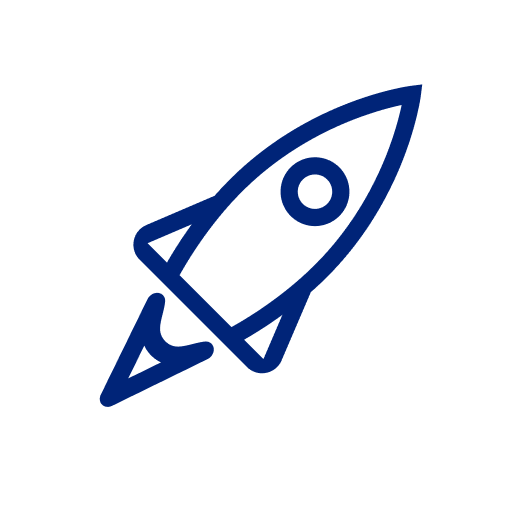
Scaling of the engineering process
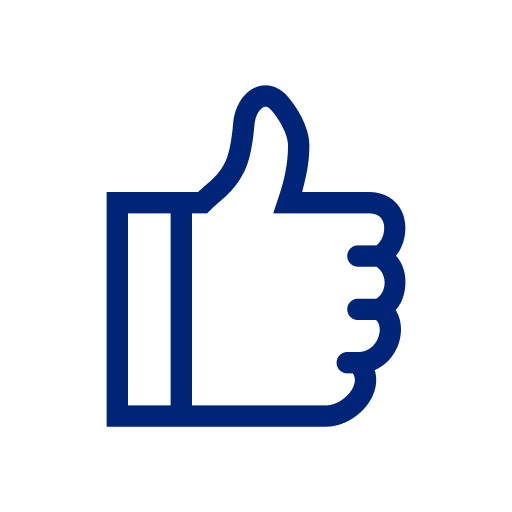
Interaction of several engineering tools