Automating solver calls to boost engineering productivity
Discover how ARRK Engineering dramatically reduced the manual workload in FE model builds by integrating a Synera workflow for applying boundary condition automatically, resulting in significant time savings and reduced human errors.
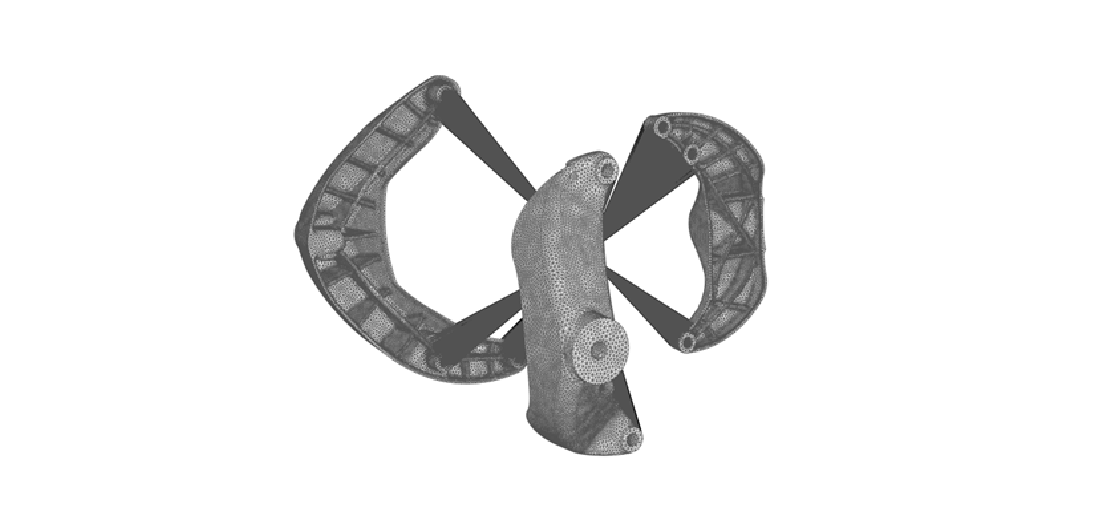
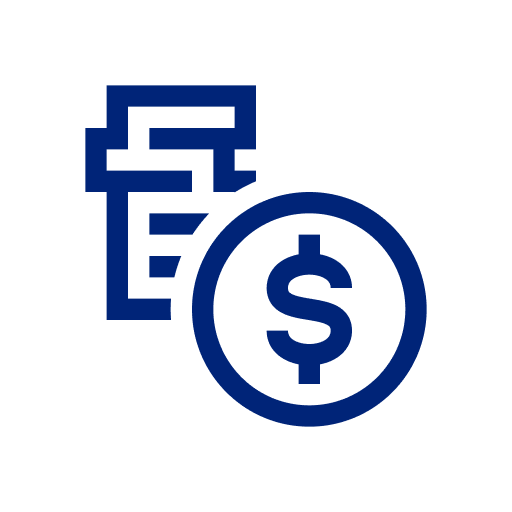
130% ROI within the first 12 months
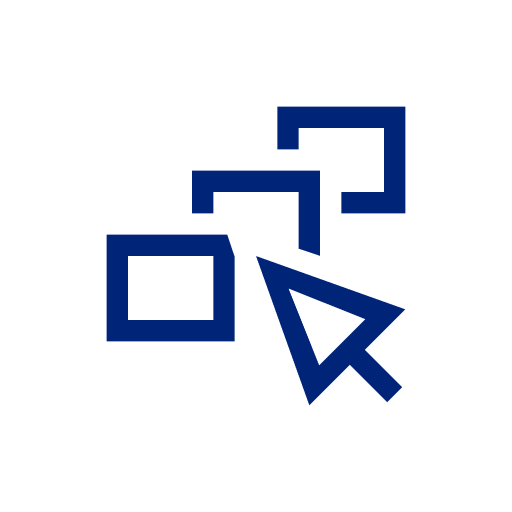
60% reduced effort in the project
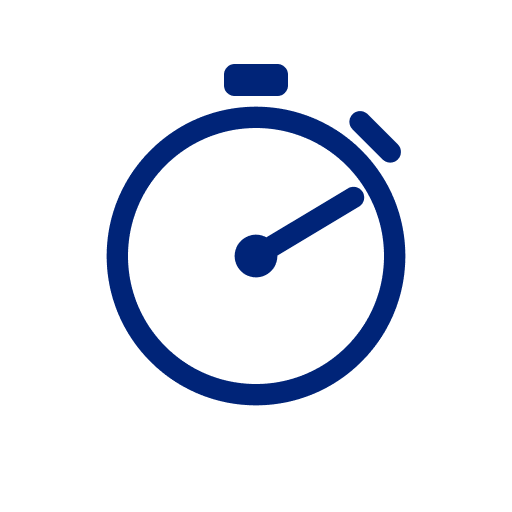
Project timeline shortened by 20%
Challenge
ARRK Engineering was managing a highly intricate process of modifying input solver decks for various finite element (FE) simulations, particularly in their EV engine mounting bracket project.
The complexity of the project stemmed from the need to handle frequent geometry updates and reassess NVH criteria, all while managing numerous load cases. Manual intervention was required to adapt to external changes, such as adjustments in bushing positions or the properties of electrical units, making it essential to configure the solver decks accurately for each update.
The existing process required engineers to manually modify input decks, which involved a deep understanding of the input structure for different solver technologies. While effective, this manual approach was time-intensive and required meticulous attention to detail, especially when ensuring the correct application of each change. Each modification needed to be followed by manual solver calls and configuration, adding further complexity as ARRK worked to maintain agility in response to evolving design requirements.
ARRK Engineering sought to automate these manual processes, reducing the need for hands-on intervention while ensuring consistency, accuracy, and speed in the delivery of project results. By doing so, the team aimed to automate workflows, maintain a high standard of engineering quality, and meet the demanding timelines of complex projects with ease.
The automation of input deck modifications and solver calls reduced our manual workload by 60% and sped up model building. This has enabled us to efficiently manage complex projects, meet deadlines with higher accuracy, and improve output quality—all through connecting pre-coded node blocks in Synera.
ARRK Engineering GmbH
ARRK Engineering is a global development partner for automotive and mobility, offering end-to-end support for product development. This includes concept phase, series development, validation, and integration of mechanical and electronic components. Our expertise extends to e-mobility, autonomous driving, and software development in a digitalized environment. Efficient project management ensures we meet development goals with our customers.
Solution
An FE engineer built in less than 2 days a workflow by using the Synera Low-CodeProcess Automation platform, which leverages Low-Code technology. The workflow automated the modification and optimization of input solver decks, significantly improving ARRK’s efficiency. When changes in bushing positions or electrical unit properties as mass, CoG or inertia occurred, Synera automatically extracted the new values and updated the input decks for dynamic mount simulations. These modified decks were then automatically pushed to a high-performance cluster where simulations were performed using Abaqus. If the mount system failed to meet performance requirements, Synera optimized the inputs and reran the simulations until the criteria were met.
The successful integration of the new bushing characteristics into a CAD manipulation sub-workflow ensured that the original CAD geometry was morphed to not only meet the updated requirements but also checking the manufacturing feasibility of the morphed geometry. The new geometry was checked by a final FE simulation, followed by an automated FE report creation. This automated workflow was made accessible to CAD engineers via an internal server through Synera Run, allowing them to perform simulations for concept designs efficiently. With that the required time for concept designs was reduced from days to minutes, enabling ARRK to meet tight deadlines and maintain high-quality outputs.
More about this workflow
Benefits
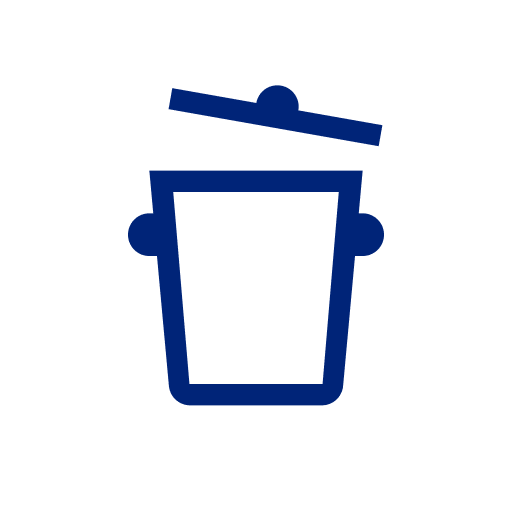
Avoidance of manual errors

Decreased model build time
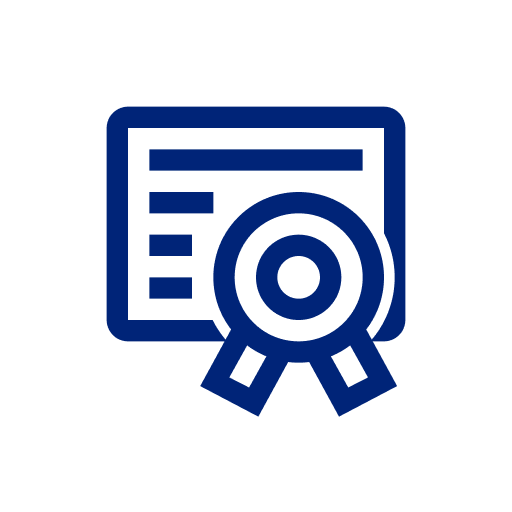
Knowledge storage through digitization of engineering
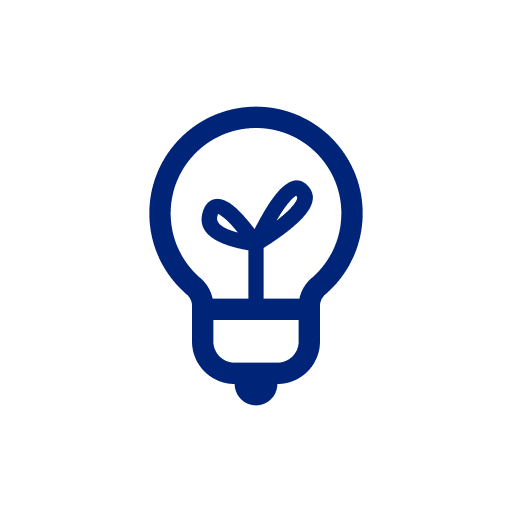
Enhanced understanding of impact changes
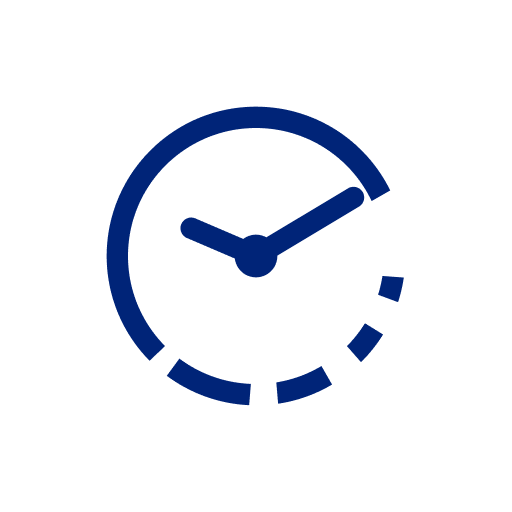
Reduction of Time-to-Market