Enhanced 3D-printed gripper design
The BMW Group, a leader in automotive additive manufacturing, leverages Synera’s process automation software to optimize the design and expands the use of its 3D-printed, customized robot grippers. This resulted in a significant increase in production speed, product durability, and reduced CO2 emissions.
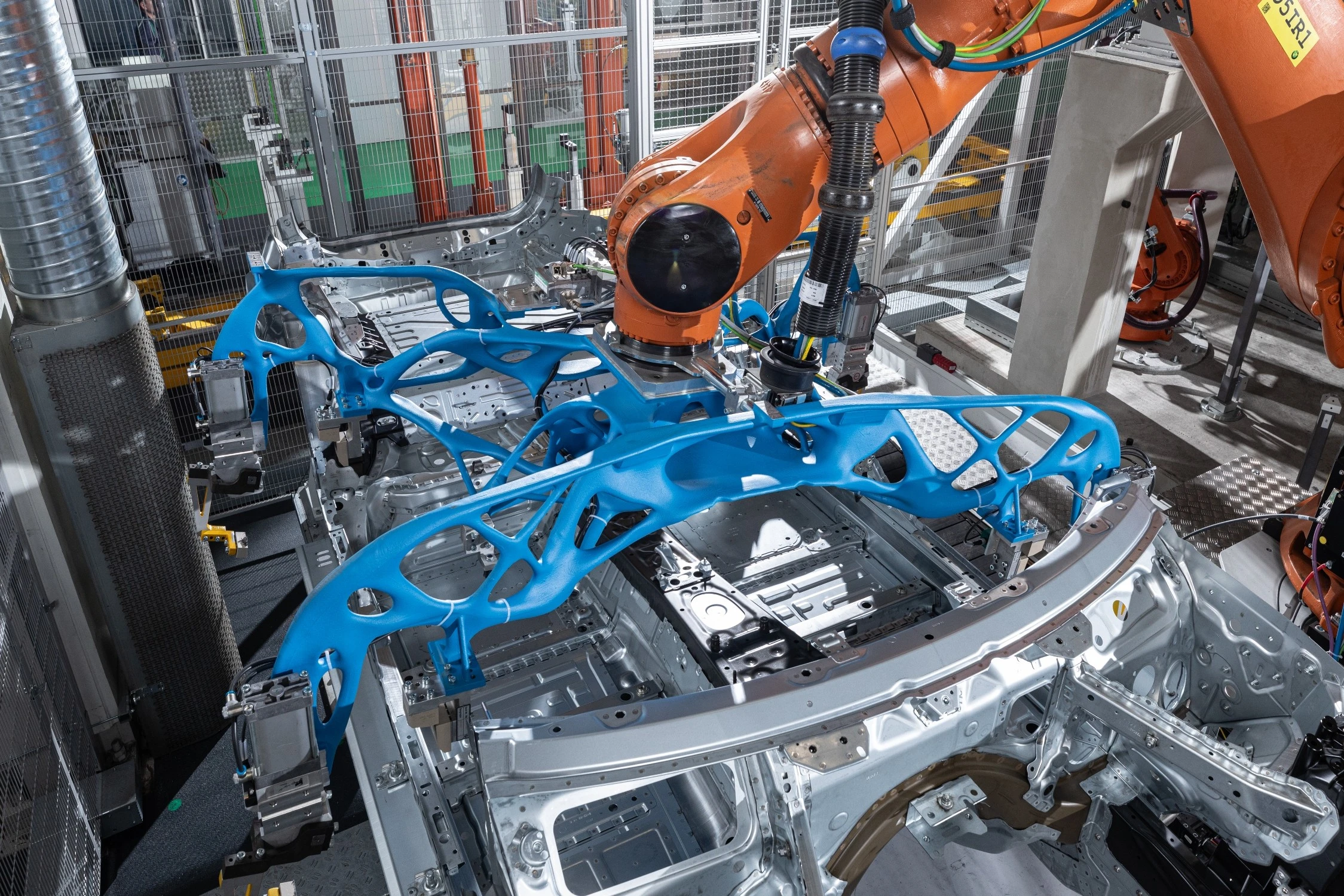
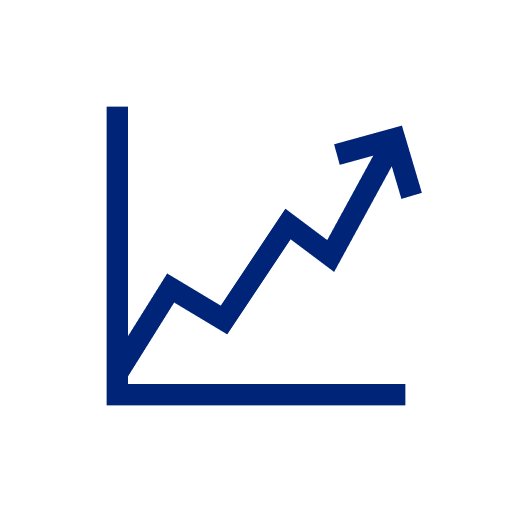
30% weight reduction
extending robot operating life and reducing system wear.
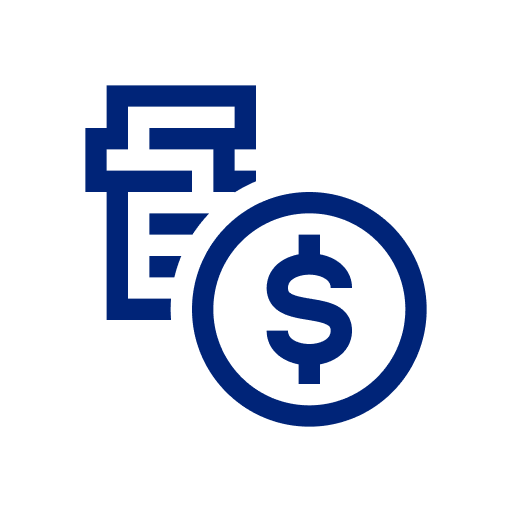
Decrease in production time & costs
gripper manufactured in 22 hours using 3D printing.
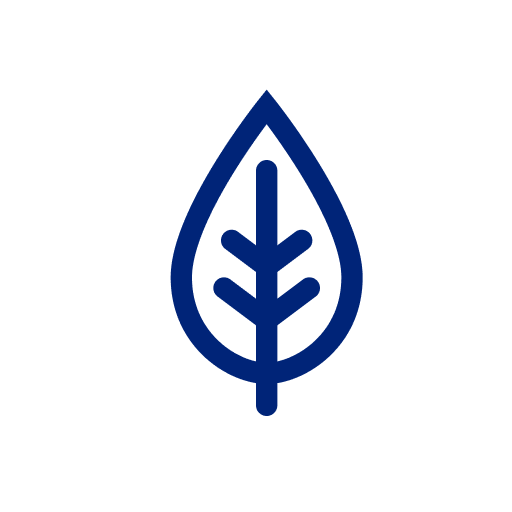
60% CO2 emission reduction
compared to conventional methods.
Challenge
The BMW Groups’ leadership in Additive Manufacturing
For over three decades, the BMW Group has led the automotive industry in additive manufacturing innovation. Since its pioneering use of 3D printing technology in 1991 for concept cars and prototypes, the BMW Group has continually expanded its application to production models and essential production aids. Today, their Additive Manufacturing Campus in Oberschleißheim serves as a hub for research, development, and training in 3D printing, producing over 300,000 parts annually across global production sites.
Innovating amidst manufacturing complexity
The automotive manufacturing landscape presents a myriad of complex challenges, from stringent quality standards to the need for rapid production cycles and cost efficiency. The BMW Group recognized the imperative to innovate and enhance its manufacturing processes to maintain its competitive edge in a dynamic market.
To enhance efficiency, the BMW Group looked at optimizing the production of robot grippers used in handling tasks such as CFRP roof assembly and chassis construction. These grippers play an important role in maintaining efficiency and precision across the BMW Group’s production lines, demanding solutions that could shorten manufacturing cycles, reduce costs, and enhance operational flexibility without compromising quality.
We are able to quickly, economically, and flexibly produce our own production aids and handling robots, which we can individually adapt to specific requirements at any time, as well as being able to optimise their weight. Less weight allows higher speeds on the production line, shorter cycle times and reduced costs.
BMW Group
With its brands BMW, MINI, Rolls-Royce and BMW Motorrad, the BMW Group is the world's leading manufacturer of premium automobiles and motorcycles and a provider of premium financial and mobility services. The production network of the BMW Group comprises more than 30 production locations worldwide; the company has a global sales network with representatives in more than 140 countries.
Solution
Automating design workflows with Synera
The integration of Synera’s process automation software at the BMW Group’s Additive Manufacturing Campus has led to a significant improvement in manufacturing efficiency. By utilizing advanced algorithms and topological optimizations, Synera enables BMW engineers to design lightweight, robust grippers that meet the specific requirements of each production task. The software is particularly beneficial for 3D printing, as it allows for the direct printing of topologically optimized, bionic structures due to the high flexibility of the 3D printing process.
In gripper design, Synera’s specialized workflows automate the creation and calculation of complex bionic structures, making the process fast and efficient. By automating complex design processes and optimizing material usage, the BMW Group has reduced the manufacturing time of grippers to just 22 hours—a notable improvement over traditional methods. The ability to produce grippers quickly and efficiently allows the BMW Group to respond swiftly to changing production needs and demands, increasing flexibility in their manufacturing processes. The lighter weight of the grippers enhances the speed and agility of the robots, reducing wear and tear and extending their lifespan, which lowers maintenance costs.
This comprehensive approach to design and production optimization demonstrates the BMW Group's commitment to innovation and operational excellence. By streamlining complex design processes and optimizing material usage, Synera’s software is now used in many development areas within the BMW Group, driving efficiency and performance across their manufacturing operations.
Read the latest press release from the BMW Group to learn more about our exciting project together: https://www.press.bmwgroup.com/global/article/detail/T0442351EN/bmw-group-expands-use-of-3d-printed-customised-robot-grippers
More about this workflow
Benefits
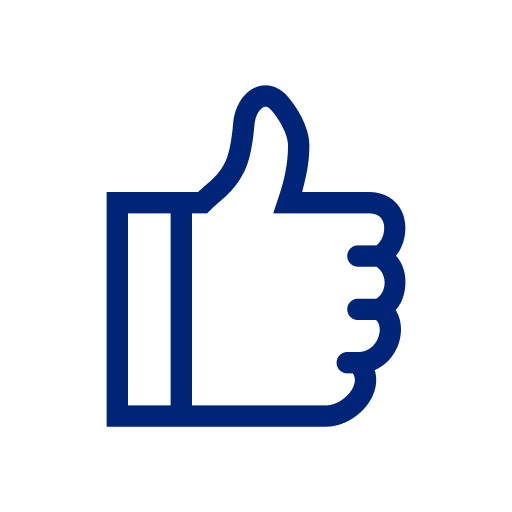
Higher quality products
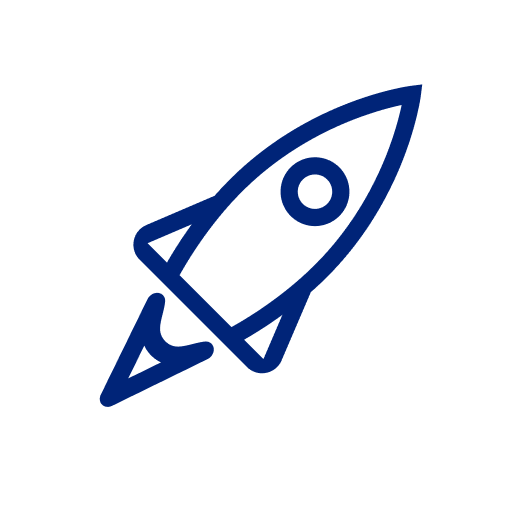
Reduced development effort
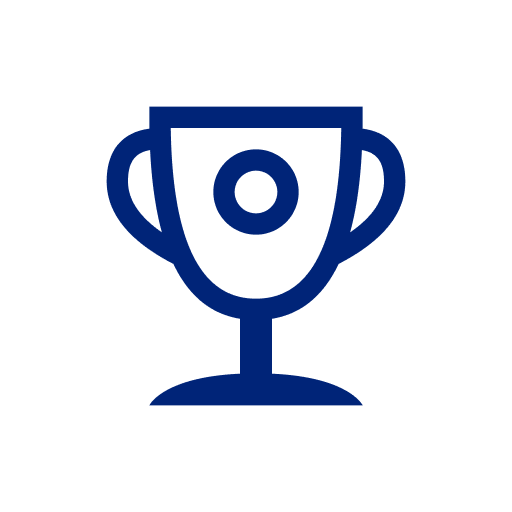
Reduction of hardware costs
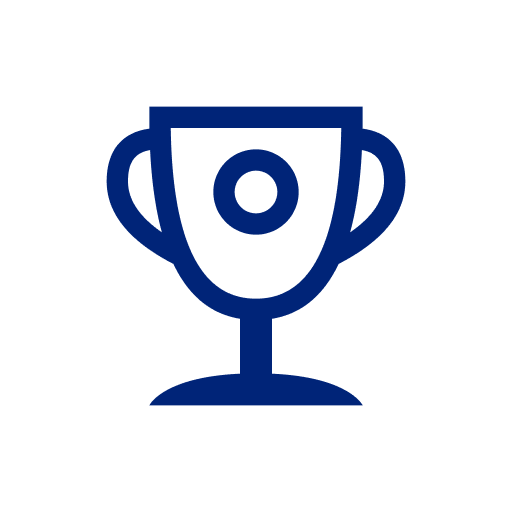
Streamlined design process for maximum efficiency