Bridging Full Automation, Tools and Human Expertise
Cut down on complexity for cost engineering
Discover how to reduce the complexity typically associated with cost engineering by managing multiple data sources and tools. The intuitive user interface and the open software platform allow to unify fragmented data sources of engineering experts and integrate industry-standard tools into one automated process. This approach delivers precise, real-time estimates for component costs and CO2 emissions that increase the efficiency of purchasing departments.
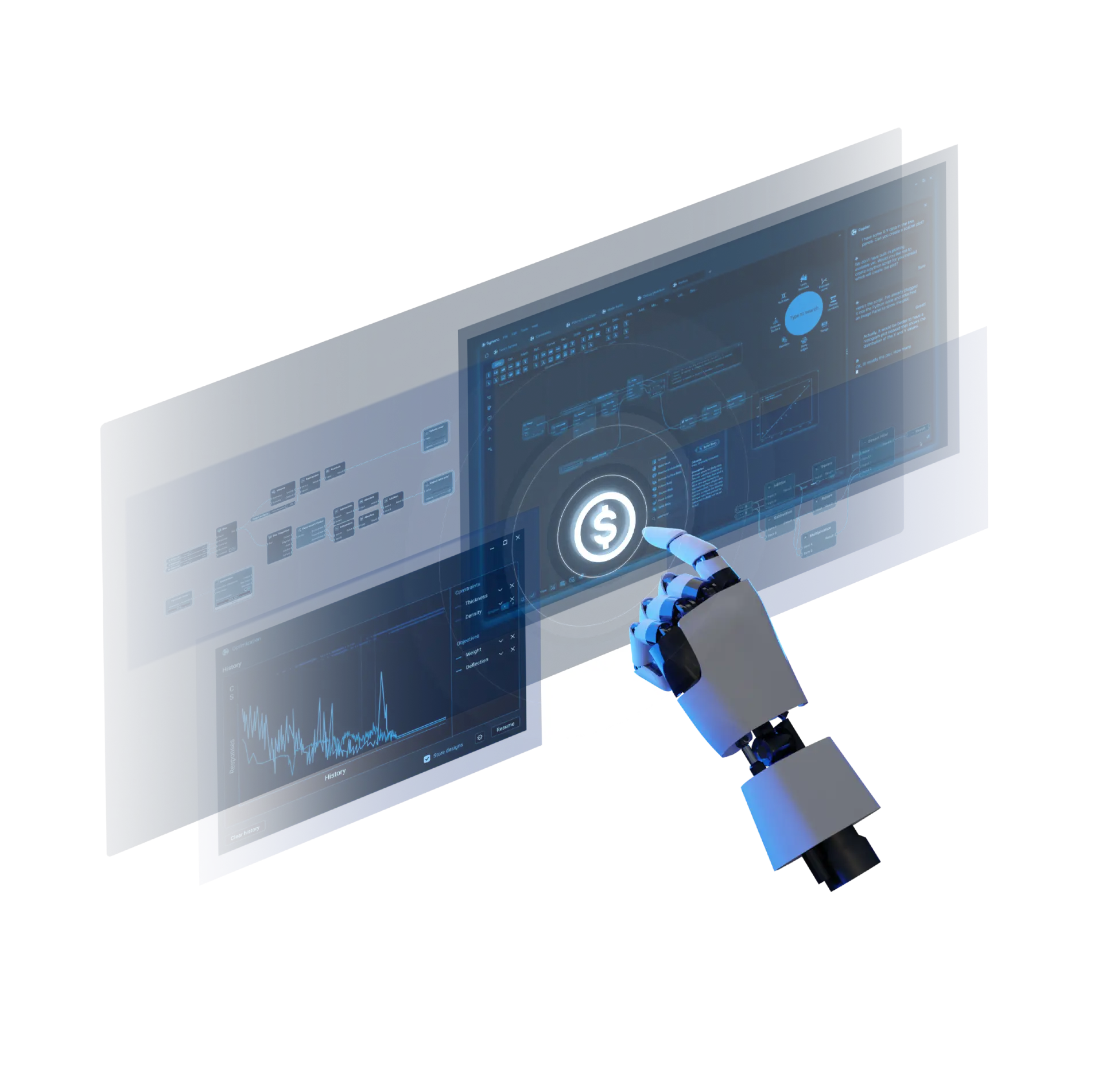
Challenge
Modern cost engineering faces the challenge of integrating a variety of tools, from spreadsheets and custom software and API calls to web-based services and specialized CO2 footprint databases. While these tools possess unique capabilities, the flow of information and data also introduces complexity to cost estimations.
The difficulty largely stems from the fact that various departments utilize distinct tools and methodologies. Coordinating data sharing, aligning meetings, and waiting for expert input become necessary steps, which can introduce potential delays. The responsibility falls on the cost engineering team to navigate such a multifaceted environment. Their expertise guides decisions on matters like identifying the most cost-effective manufacturing technique based on production volumes.
Unfortunately, due to these complexities, finalizing a single pricing estimate can take extensive amounts of time - sometimes hours or even days. Such delays significantly hinder the purchasing department's ability to acquire components at favorable costs. Additionally, the system’s dependence on individual expertise poses a risk. If an expert departs, there's a potential knowledge gap, challenging the scalability and efficiency of the cost engineering process. Emerging technologies like AI-based predictive pricing models are yet to gain full acceptance. They often lack a rule-based framework that can serve as a plausibility check. This shortfall makes departments hesitant and leads them to rely on potentially outdated historical costs.
"Our service has transformed the cost evaluation landscape. Synera's live link between geometric data and costing tools empowers engineers with accurate insights, leading to optimal decisions in component costs. This collaboration directly supports purchasing and results in significant cost savings."
ARRK Engineering GmbH
ARRK Engineering is a global development partner for automotive and mobility, offering end-to-end support for product development. This includes concept phase, series development, validation, and integration of mechanical and electronic components. Our expertise extends to e-mobility, autonomous driving, and software development in a digitalized environment. Efficient project management ensures we meet development goals with our customers.
Solution
Synera streamlines cost engineering by effectively combining automation with human expertise. Central to the platform design is the ability to capture and reuse fragmented expert knowledge and data from various software tools. These elements are then integrated into automated workflows, setting the stage for more reliable and intellectually informed decisions.
Building on this foundation, the open API architecture offers another layer of adaptability. It supports straightforward integration with industry-standard tools like FACTON, thus fitting effortlessly into an existing tech stack. This makes it easy to adapt to specific pricing and procurement needs. And the system's built-in CAD capabilities allow for in-depth geometric analyses, yielding highly accurate estimates for costs and CO2 emissions.
Due to this integrated approach and multi-faceted feature set, Synera significantly cuts down on the complexity that is typically linked to cost engineering. Tackling complexity in engineering doesn't require sacrificing a user-friendly experience. The canvas style interface allows cost engineers to effortlessly set up automation workflows using a drag-and-drop approach that requires no programming skills. This user-centric approach not only simplifies workflow creation but also facilitates real-time process documentation and debugging, thereby reinforcing transparency and trust.
The recent introduction of Synera Run extends the reach of the platform and simplifies its use even further, allowing workflows to be executed by stakeholders who are not Synera experts. The workflows can be executed easily in a web interface, based on a RestAPI. With just a few inputs like part numbers and volumes, users can obtain immediate, precise data on part costs, tooling costs, and CO2 emissions. This feature is particularly beneficial for procurement teams, enabling quick and reliable access to cost estimates. In summary, Synera doesn't merely automate tasks. It acts as a comprehensive solution that refines and enhances the entire cost engineering process, making it more efficient, scalable, and reliable.
More about this workflow
Benefits
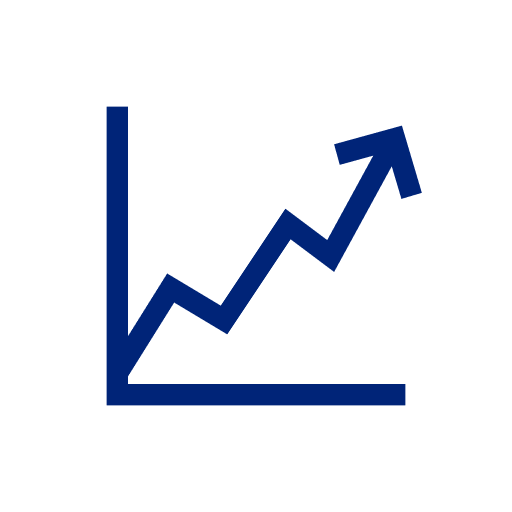
Full automation with multi-tool integration
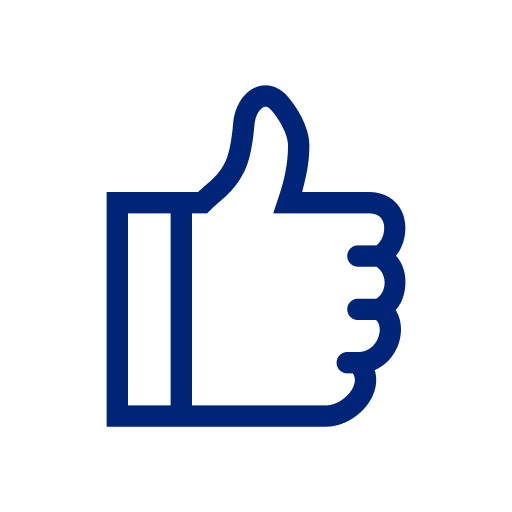
Intuitive user interface for easy execution of complex tasks
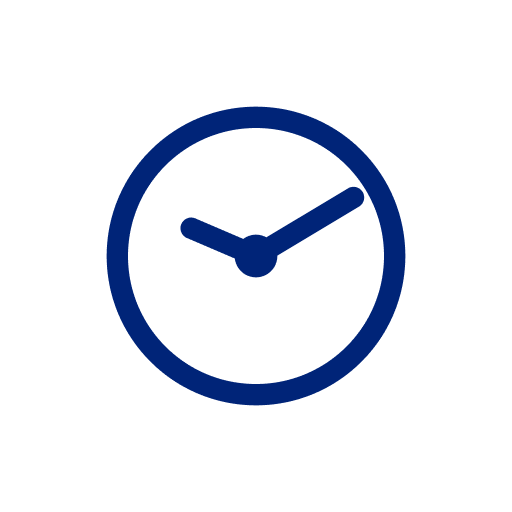
Save development time and cost through automation
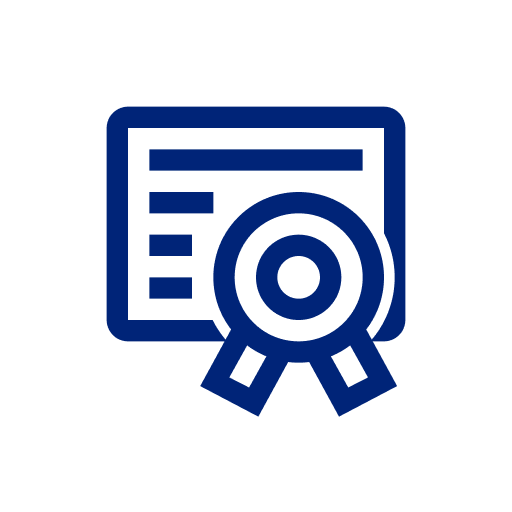
Transparency and Trust through documentation and debugging features