Enhancing FE model build efficiency
Discover how RLE International dramatically reduced the manual workload in FE model builds by having their engineers automate the steps of applying boundary condition through Synera's process automation platform, resulting in significant time savings and reduced human errors.
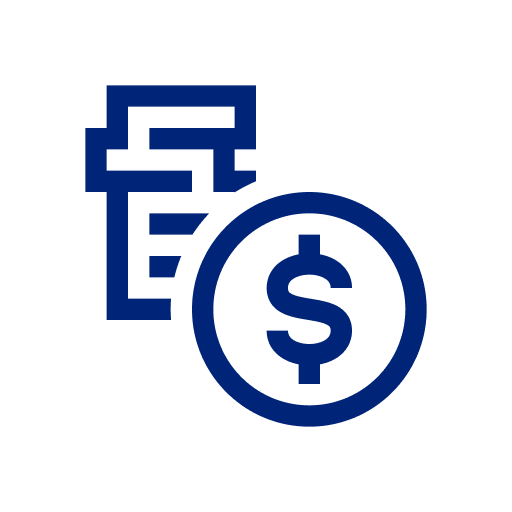
320% ROI within the first 12 months
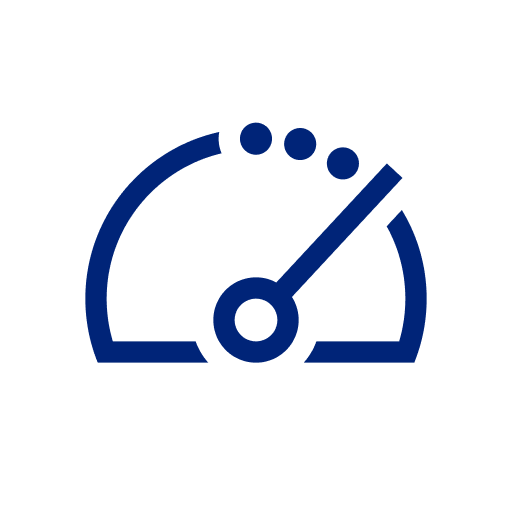
Model building time reduced by 30%
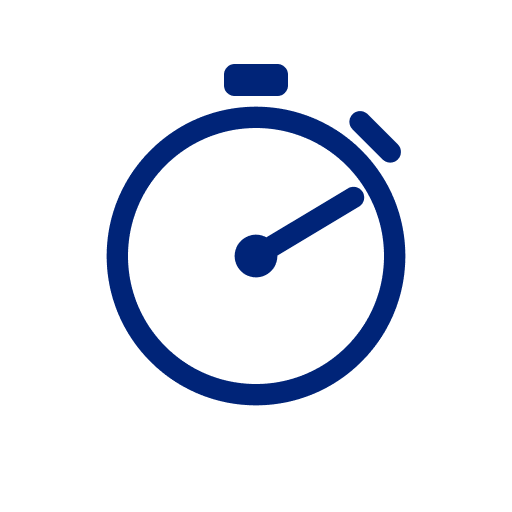
5% higher added value in Germany
Challenge
RLE International faced significant challenges in their FE model building process, the status quo involved click-intensive and time-consuming manual work that was hard to scale, hindering the move towards shorter development cycles. Initially the choice was to outsource to best cost countries, which while more affordable came with its own downsides. The feedback on simulation results took an extensive amount of time, slowing down overall product development.
In the specific context of chassis development, RLE often needed to apply hundreds of load cases, a task that became especially challenging when late-stage changes were introduced. These late changes made it difficult to adhere to tight project timelines and risked delays in the release of hardware tooling, which could jeopardize the start of production (SOP) schedules for vehicles. Managing these extensive load cases manually was not only error-prone but also significantly slowed down the entire development process and making it harder to meet critical deadlines.
By leveraging Synera’s automation, we reduced the number of engineers needed for FE modeling from 5 to just 3. The automated application of boundary conditions has not only decreased manual errors but also accelerated our build times by 30%, allowing us to react faster to last-minute changes without sacrificing quality.
RLE INTERNATIONAL
The RLE INTERNATIONAL Group is one of the world's leading providers of development, technology and consultancy services to the international mobility and services industry. RLE has over 30 years of experience in developing innovative and effective solutions for its international customers. More than 2,000 employees worldwide keep abreast of technological advances.
Solution
Adopting Synera enabled RLE to change their FE model building process by automating the application of boundary conditions. As Well as the specific solver runs (Optistruct, Abaqus or LS-Dyna) and automated PPT reporting of contour plots and Component KPIs. This automation was achieved by a CAE engineer without programming knowledge, using the visual Synera programming language. The solution allowed CAD designers to add attributes to surfaces with a single click, which indicated where specific boundary conditions, such as force or fixed displacement, should be applied. These attributes were automatically read and sorted by Synera when the CAD model was loaded. During meshing, Synera searched for nodes within a specific tolerance to the filtered surfaces and applied predefined boundary conditions based on the rules associated with the attributes. This automation significantly reduced manual errors and model build time, facilitating faster development cycles and allowing the value chain to be transferred back to the main development site.
Moreover, Synera's automated workflows and rules-based application of boundary conditions transformed the efficiency of handling extensive load cases. Load cases could be read from an Excel list and easily modified, reduced, or extended, streamlining the process significantly. This adaptability ensured that even with late-stage changes, RLE could maintain timelines and meet hardware tooling release schedules, safeguarding the SOP for vehicles. With that, the automated approach not only improved precision and reduced errors but also increased overall efficiency, enabling faster iteration and feedback cycles.
More about this workflow
Benefits
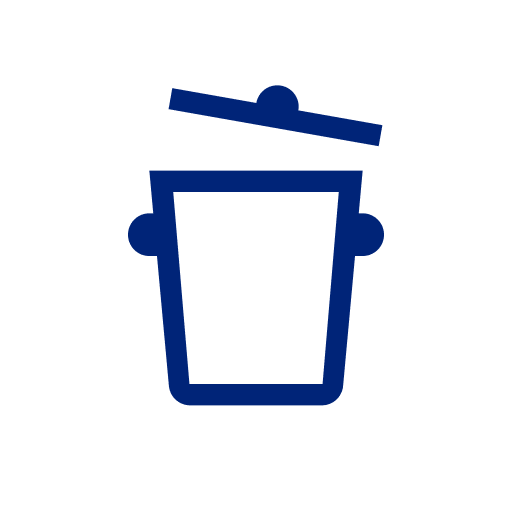
Avoidance of manual errors

Decreased model build time
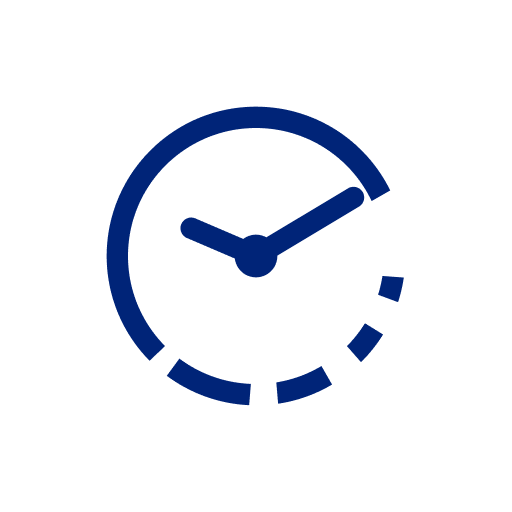
Reduction of Time-to-Market
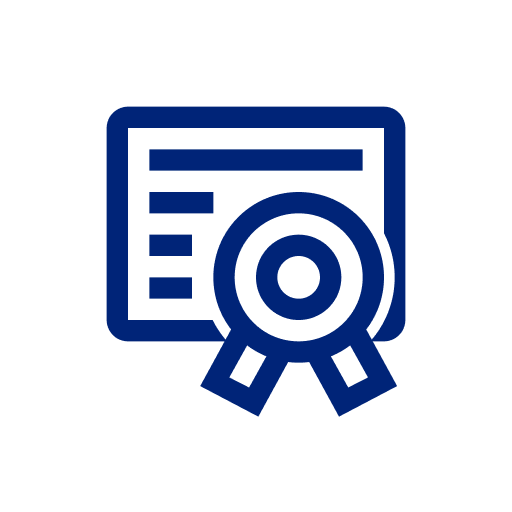
Knowledge storage through digitization of engineering
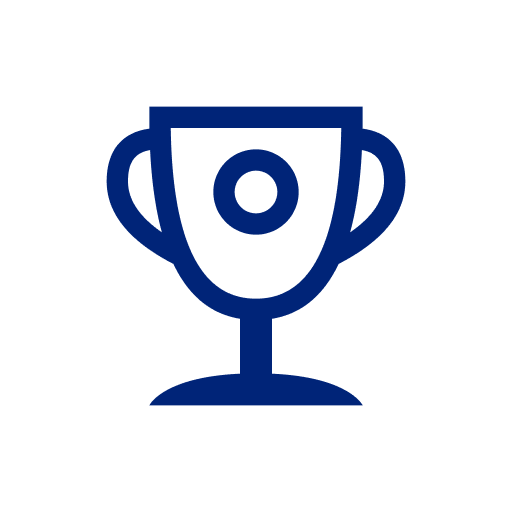
Faster CAE response