The BMW Group is enhancing its production capabilities by optimising 3D printed robotic grippers using Synera's process automation software. This approach has led to increased production efficiency, longer product life and reduced CO2 emissions. The company has been using 3D printing since 1991, initially for prototype and concept cars, and now for mass production and various tools used in its own manufacturing processes.
To remain competitive in a dynamic market, BMW wanted to optimise the production of robotic grippers used in tasks such as assembling CFRP roofs and other components. These grippers are critical to maintaining the precision and speed of BMW's production lines. By switching to 3D printed, weight-optimised versions, BMW has achieved significant improvements. For example, a 120kg gripper produced in just 22 hours is used in roof production and is 20% lighter than conventional models, leading to longer robot life and reduced maintenance.
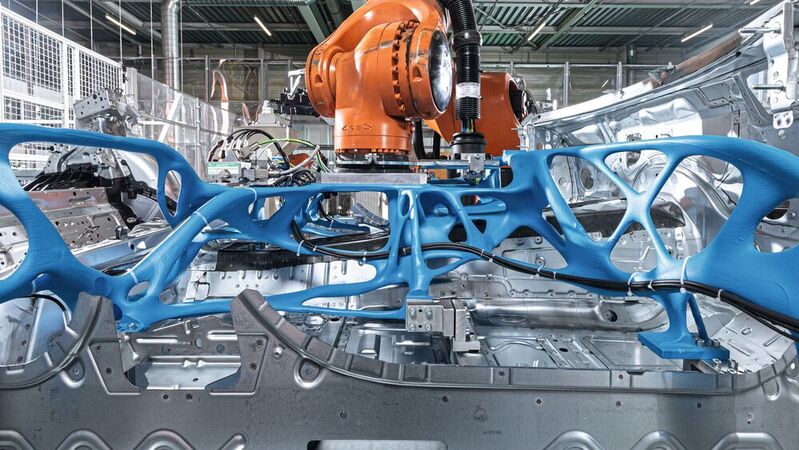
In mid-2023, BMW introduced a new generation of bionic grippers that are even lighter - 25% less than the previous design. This innovation, which combines advanced 3D printing techniques and topology optimisation, allows a single robot to perform tasks that previously required three. The Landshut plant now uses dual grippers for CFRP roofs, all of which are customised in-house using 3D printing.
BMW is also using these 3D printed grippers in body shop for tasks such as handling doors and moving entire floor assemblies. One gripper at the Munich plant, optimised using a sand casting process, weighs just 110 kg - 30 per cent lighter than conventional models. This reduction allows BMW to use smaller, lighter robots that consume less energy and contribute to lower CO2 emissions.
Synera's process automation software plays a key role by automating the design and calculation of these complex bionic structures. The software is integrated directly into BMW's Additive Manufacturing Campus, enabling engineers to create lightweight, customised grippers tailored to each task. This automation speeds up production, reduces material waste and increases operational flexibility. Overall, the reduced weight of the grippers results in faster robot movement, less wear and tear, and longer system life.
Using 3D printing and advanced software, BMW has transformed its production processes to achieve greater efficiency, cost savings and sustainability.