Automating Engineering Workflows: Insights into Meshless FEA and Process Automation
Simulation technologies' evolution continues redefining how engineers design, analyze, and innovate. In this discussion, Jousef speaks with Rik Baruah, a pioneer at Intact Simulation, about the groundbreaking possibilities of Meshless FEA technology and its seamless integration with Synera’s low-code process automation platform. Together, they explore how eliminating traditional bottlenecks like meshing and incorporating advanced automation tools can unlock unprecedented efficiency and creativity in engineering.
Meshless FEA: A New Paradigm for Engineering Simulation
Traditional Finite Element Analysis (FEA) methods involve time-consuming processes like meshing, which require engineers to simplify models, remove small features, and navigate multiple iterations to achieve accurate results. This approach often limits the speed and flexibility needed in modern engineering.
Meshless FEA eliminates these challenges by decoupling the simulation process from geometry meshing. Using a 3D grid to mesh the space around the geometry rather than the geometry itself, Intact Simulation’s technology can handle complex structures like lattices without requiring simplification. The result is a dramatic improvement in efficiency:
- Traditional simulations often take 2.5 hours; meshless FEA achieves the same results in less than 5 minutes.
- Complex geometries, such as engine blocks with intricate features, can be analyzed directly without compromising accuracy.
These advancements are not only reshaping the role of simulation but also cutting development timelines by up to 50%, enabling faster decision-making and significant cost savings.
Automating Simulation Workflows with Synera
Synera’s low-code platform perfectly complements Intact Simulation’s meshless FEA technology. Integrating seamlessly with existing engineering tools, Synera enables engineers to automate repetitive tasks and streamline workflows without requiring extensive programming skills. Key benefits include:
- Faster Iterations: Configure simulations with a few clicks and automate parameter sweeps for rapid design exploration.
- Seamless Integration: Synera’s marketplace includes a direct module for Intact Simulation, allowing users to set up simulations within their existing workflows effortlessly.
- Scalability: Automate large-scale simulations while maintaining flexibility to adjust parameters as needed.
Integrating meshless FEA directly into Synera’s low-code environment democratizes simulation capabilities, empowering a broader range of users, from design engineers to industrial designers.
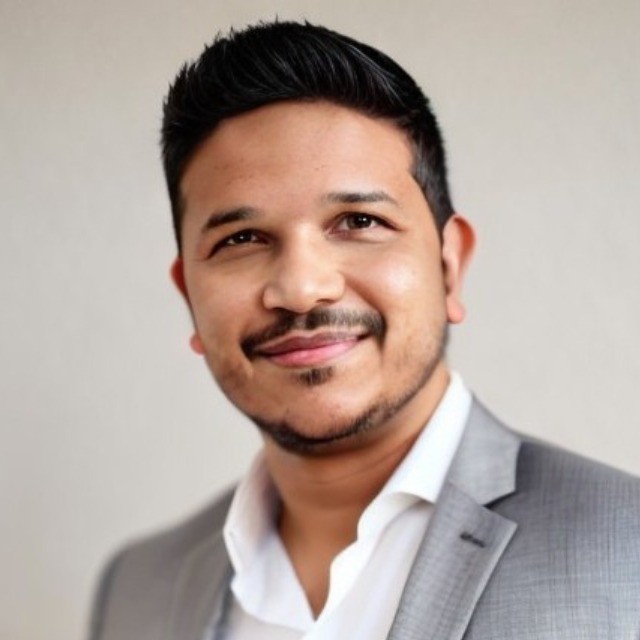
Unlocking Advanced Use Cases with Meshless FEA
Meshless FEA stands out in handling use cases where traditional FEA tools often fall short. Notable applications include:
- Lattice Structures: Simplify workflows for validating complex lattices without requiring manual meshing.
- Engine Components: In one example, an engine block simulation using meshless FEA achieved results within 3% of traditional methods, cutting simulation time to 5 minutes.
- Process Automation: By embedding Intact Simulation’s technology within Synera, engineers can connect to additional tools like CAD systems or manufacturing analysis modules for end-to-end workflow automation.
These capabilities streamline workflows and free engineers to focus on high-value tasks like design innovation and optimization.
AI-Driven Simulation and Design Optimization
Intact Simulation is taking the benefits of meshless FEA a step further by integrating AI and machine learning into its workflows. By generating vast amounts of simulation data, engineers can:
- Optimize designs for manufacturability, cost, and material constraints.
- Explore entire design spaces and predict failure modes with greater precision.
- Use AI to analyze real-time sensor data, enabling predictive maintenance and damage assessment.
For example, in a DARPA-funded additive manufacturing project, Intact uses AI to optimize designs based on process parameters like laser speed and power. Integrating physical testing and historical data ensures that designs meet manufacturing constraints without sacrificing performance.
Bridging Education Gaps and Scaling Automation
One of the goals of Intact Simulation and Synera is to democratize engineering simulation. While traditional FEA workflows often require specialized expertise, meshless FEA and low-code automation make these tools accessible to a wider audience, including:
- Design Engineers and Industrial Designers: With user-friendly interfaces and minimal setup, these professionals can quickly integrate simulation into their workflows.
- FEA Engineers: By automating repetitive tasks, experienced analysts can focus on high-impact projects and expand their responsibilities.
Synera and Intact Simulation integration ensures that simulation can move upstream in the product lifecycle, reducing iteration cycles and driving innovation.
A Vision for the Future of Engineering
As Rik from Intact Simulation emphasizes, the future of engineering lies in collaboration and interoperability. No single tool can solve every problem, but integrating the right technologies can transform workflows and accelerate product development. By combining meshless FEA with Synera’s process automation, organizations can create a digital thread that spans concept design, simulation, and manufacturing.