Everyday life for the engineer: A technical component, e.g. a grid tube construction, must be designed as optimally as possible into a defined design space. The developer has to optimize the mechanics, achieve a minimum weight, at the same time use semi-finished products that are as cost-effective as possible and optimize the length of the welding seams in order to reduce the manufacturing costs. But how does he achieve this ambitious goal in the shortest possible time?
In the classic development process, the engineer approaches the solution to this problem step by step. He starts with a concept draft, designs it and evaluates it. Then iterates manually between the development phases.

This procedure is mostly characterized by manual data conversion between different software tools, waiting for simulation results from other departments and manual CAD construction. The further you move backwards in the development process, the more difficult it becomes to change fundamental decisions such as the manufacturing process used. At the same time it is difficult to estimate the final costs in early stages of development and thus to set the right course from the beginning. Last but not least, this process is characterized by the coordination of the many interfaces between experts from different disciplines. Decisions often have to be made using “educated guess” because the necessary facts are not (yet) available.
Engineers were once the creators of the great solutions of tomorrow. But in today’s processes, we spend a large part of our working time on recurring everyday tasks and coordination of the interfaces, and so it is difficult to produce really great innovations because we simply do not have the time.
If we engineers could wish for something…
For all Marvel fans, the artificial intelligence J.A.R.V.I.S. developed in Iron Man by Tony Stark is certainly a software with which we would like to develop new products together. Jarvis supports Tony in the development of new technical solutions, provides him with answers within seconds about the performance of design alternatives and optimizes existing systems fully automatically.
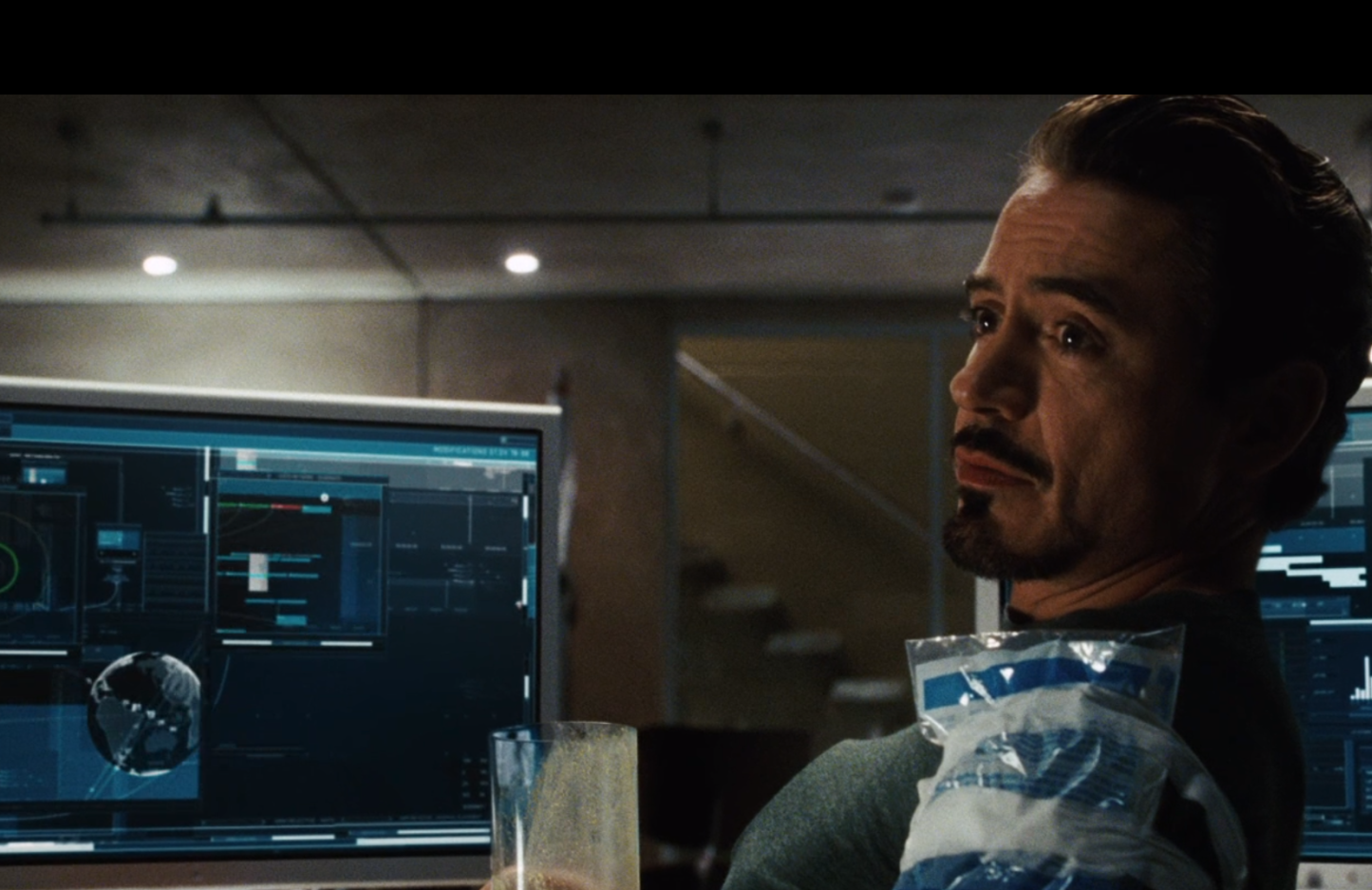
Although we are still a long way from this vision, the first steps in this direction are already being taken. In the future, engineers will be able to use computers to develop optimal products automatically – this new approach to product development is called generative engineering. The method uses intelligent algorithms and automates recurring processes that developers have so far done manually. This technology allows the design of components to be automated. On the one hand, this is much faster and sometimes the algorithms come up with even better solutions than we humans do.
Intelligent algorithms deliver solutions without human intervention
In generative engineering, the engineer can define complex problems in the form of several clear design rules, limits and target values and store them in algorithms: In the example mentioned at the beginning, these algorithms are supposed to find the optimal geometry that can just about withstand the required loads and at the same time connect the most cost-effective semi-finished products with as few and short welding seams as possible and can therefore be implemented as cost-effectively as possible.
We call this set of rules modeled with algorithms how the component is to be created a “technical DNA”. Similar to nature, it contains all the rules according to which the component can “grow”. The DNA thus represents a logic that enables adaptation to changed boundary conditions – just as it is possible for organisms in nature.
To ensure that all the necessary factors that influence the geometry of the construction can be taken into account, it is necessary that all engineering tools are integrated and networked in this DNA. This includes not only the generative tools (e.g. CAD or also Generative Design solutions) but also the evaluating tools (e.g. FE simulations, cost evaluations and manufacturing simulation).
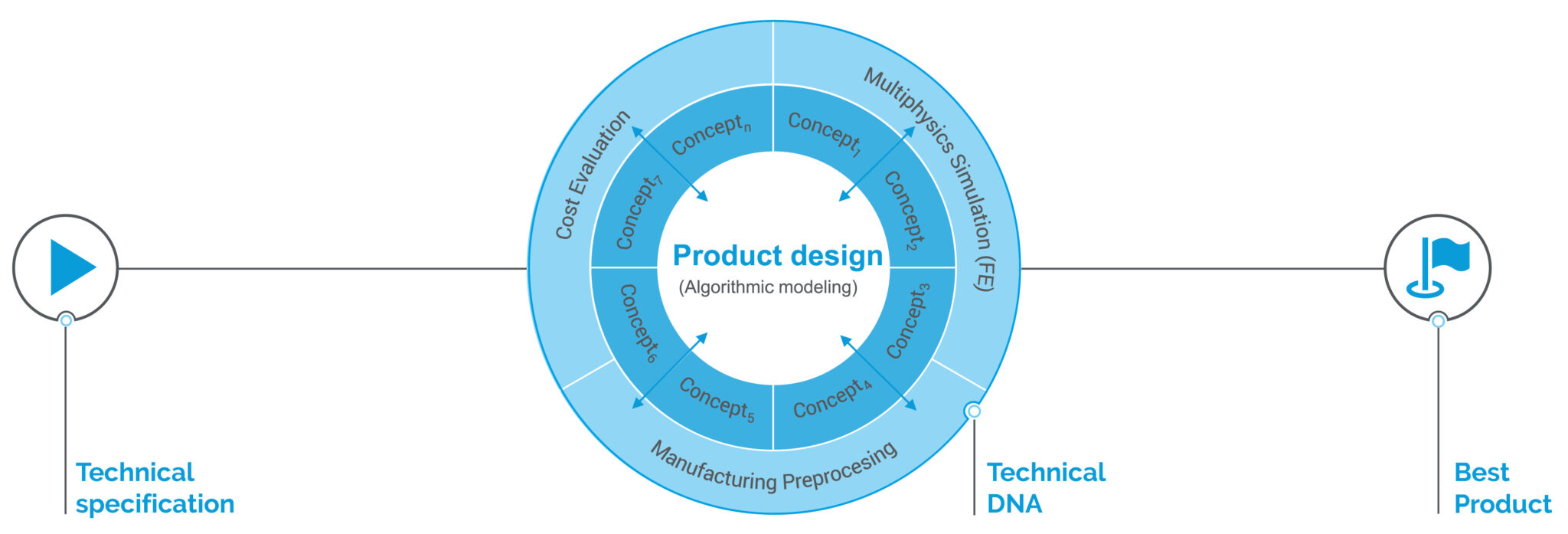
Storing the set of rules in a technical DNA allows not only to secure expert knowledge but also to fully automate the design process, making it much faster. The technical DNA is created by an expert. He obtains all project-relevant data in advance and digitizes it in the form of a coherent development process. In other words, he simply creates the set of rules in the form of the DNA, the “way to the product”. He then leaves the actual design and adaptation of the component to the boundary conditions to the intelligent software, which can “grow” the component from the DNA.
A common language for engineers
A prerequisite for the creation of a technical DNA is the networking of all tools and work steps of a product development, the so-called “Connected Engineering”. Only the interface-free interconnection of all software tools and process steps can avoid manual import and export steps that would prevent automatic generation of the solution. All departments must be able to digitize their expert knowledge in DNA and store it in a readable form for the other disciplines. To make this technically possible, a universal data model is necessary – a uniform “language” for management, development engineers, purchasing and production.
What happens if the boundary conditions should change?
Up to now, things have usually gone like this in the development departments: If the external conditions of a component change, the engineer has to start large parts of the development process from scratch. With generative engineering, everything goes much faster. Within the technical DNA, all the development steps are already present and linked together, so a computer can use the DNA to automatically generate the design adapted to the new conditions. This enables the engineer to react quickly even to late changes or have entire families of components created automatically. He only has to change parameters in the algorithm.
So in the future, the developer will no longer design each component individually. Instead, he will define a DNA that encodes the development process. He will then “plant” this DNA in various vehicles and have the algorithms generate the optimum component. In this way, the component optimally adapted to its environment is developed, it “grows” according to the specified DNA.
What will the future bring?
Generative Engineering now lays the foundation for the digital networking of expert knowledge, rules and regulations on construction methods, process steps and influencing variables, as well as all the necessary simulation tools in a machine-readable format. In the field of additive manufacturing, the direct connection and control of production is already a reality today – a big step towards Industry 4.0.
To get one step closer to our Jarvis vision, the next logical step would be to make this comprehensive data available to an artificial intelligence as learning material. These will be exciting times…